I plan on building my first Axial Flux machine and I hope for some feedback from the years of knowledge here. I plan on machining up all of the components that I am able to. I plan on building the alternator first, then deciding what size blades will be needed based on test results of the alternator.
I am starting with the rotor because I have magnets and steel now. The magnets are 22.5 degree wedges, 4" ID and 8" OD, N42SH 1/4" thick neodymium. The rotor material can be 1018 or 4140 since I have plenty of both. I also have aluminum, but my understanding is that steel will direct the flux much better.
I plan machining pockets in the steel for the magnets to sit in. I thought about putting tap holes in the magnets to hold them, but I don't know if that's a good idea. I have access to an EDM so I could burn the tap holes in, but I'm afraid that this could damage or weaken the magnets.
I am trying to keep this compact, so there is not much of a gap between magnets, only about .3" I have read that this could (will) cause flux leakage, but is it so big an issue that fewer magnets or a larger diameter would make sense?
This is what I had in mind:
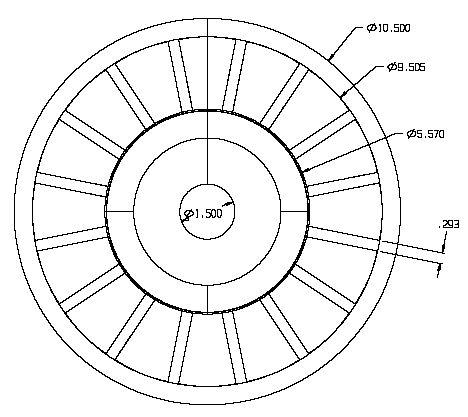
I plan on testing a few different coil configurations when I get the rotor(s) completed so I'm hoping that my cart isn't too far in front of the horse at this point.
I have been reading here and several other sites for about 6 months now, but I would have to read for a hundred years to be able to figure this all out on my own. Please take a moment and let me know what you might change. It's just on paper right now, there will never be an easier time than now to make adjustments.
My goal is to build a machine to reduce my monthly electric bill. I don't care if it costs a bit, I'm really not concerned about "payback time" since this will be part money saving, part being green, part fun, and part giving me something to tinker with when it's too cold or hot to be outside.
Thanks!