Ok, guys I need a bit of advice here. I read most of the forum discussions about casting stators, but I am still not quite sure what to do in my particular case. Working on this 10 foot other power wind turbine is the first time I have worked with any type of resin.
Anyway, I cast the 2 rotors a couple of weeks ago and they turned out great (see picture), but it was a bit touch and go. After 3 or 4 hours the resin had not started to harden at all. So, perhaps I was being impatient or stupid but I ended up putting a space heater near them and they fired off really well. I measured the temperature near the rotors and it was about 100 degrees. So I took the heater off after a few hours that night and they were totally finished hardening in the morning.
Now I am wondering what to do about my stator. I just cast it a couple of hours ago and just like before, it has not started to "fire off" at all! Am I being impatient or do I need to apply some heat to the stator now as well? I am concerned that it will crack or shrink if I apply heat like before but worry it will never cure if I do nothing. What should I do?
I used...
- 1.5 Quarts Vinyl Ester Resin
- 0.5 Quarts ATH and Fiberglass as fill (mostly ATH with a touch of fiber)
- 0.25 ounce of Hardener
It was about 85 degrees when it was cast.
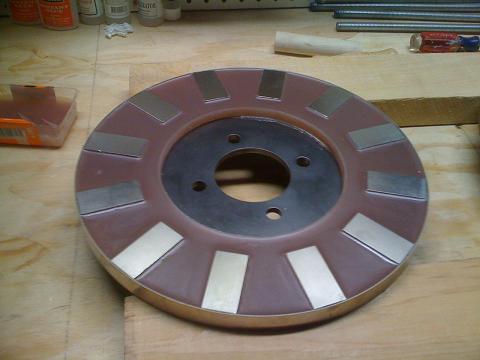
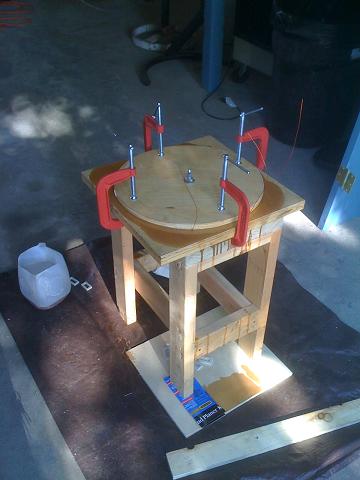