Hi Guys
A few weeks ago a member of my forum ( thabackshed ) posted a message looking for help with a small windmill he wanted to bring to market. Wes is his name, and American who has a manufacturing business in the USA, Germany and China. I contacted Wes and found out more about his windmill project. Its based on those Chinese bike hub motors, similar looking to a F&P, and readily available in China. He's rewinding the motors to suit the windmill application.
Now the interesting bit. Wes has access to PVC extrusion equipment. He's looking at extruding his own blades for his windmill, and it looks like these extrusions will also be available to the home built windmill market. Basically sold by the length PVC blades we can use on our own windmills. But Wes needs help with the best profile to use. I've made a few suggestions, seen below, but I'm no expert or experienced enough with windmill blade profiles to give the Wes the advise he needs.
I've posted a message on my site, and had some good ideas and feedback. I thought I would post the message here too, so hopefully the combination of thebackshed and fieldlines member base can come up with the best design for Wes. The backshed thread is here, its on about page 3 that the current design shows up.
http://www.thebackshed.com/Windmill/FORUM1/forum_posts.asp?TID=1331&PN=1
This is where we are at now.
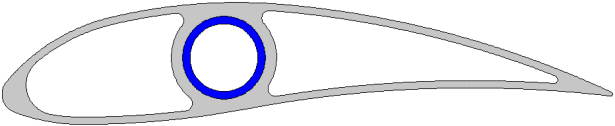
The blade shown will be extruded PVC, in this version the chord is 160mm ( sorry, its all in metric ), its 30mm fat across the middle, and thats a 22mm hole in the middle where we fit a length of steel pipe. Whats the steel pipe for? 3 reasons, 1: to give the blade strength, 2: to provide a mounting point at the hub, and 3: to allow us to twist the blade. Thats the best bit. The idea is the PVC blades can he heated and twisted around the steel pipe to give the correct angle of attack along the blade length.
This means we could buy the extruded blades in lengths ( plan is to have a few chord sizes available ), fit the steel pipe and using a heat gun ( ie the wifes hair dryer ), twist the blade to the correct angles.
Once twisted, the blade can be riveted or glued to the steel rod. There is also a winglet and end cap on the drawing board to seal off the ends.
We dont have a taper unfortunately, but thats not really an option for extruded blades and not as important as correct twist, we can live without taper.
So what Wes needs is advise on the best profile to use. Remembering we need to fit the steel tube up the middle, and we dont want a shape that will deform or buckle to easily when heated. We may need to add internal webbing to give the strength needed for twisting, would anyone have experience in heat bending plastics? And we dont want a noisy profile like those horrid Chinese fibreglass extruded blades.
What do you think? Its an opportunity for us to tell a manufacturer how to make windmill blades that will eventually be available for the aftermarket windmill guys, like us.
Glenn.