Previous post was an accidental double post.
I now have the alternator fully assembled. Here are the steps I took:
Wound all 18 coils
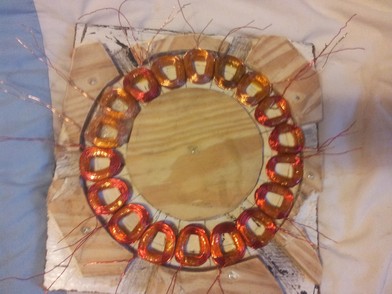
I found a use for my jig in that I could place the coils in it whilst I was fixing them together using fibreglass cloth and superglue. I found that I very slightly overwound most of my coils and they would not fit in the mould easily at the diameter they were supposed to, but at one slightly larger.
A bit of manipulation into the jig squashed them into the diameter that they were supposed to be on, and then I glued them so that they stayed that way.
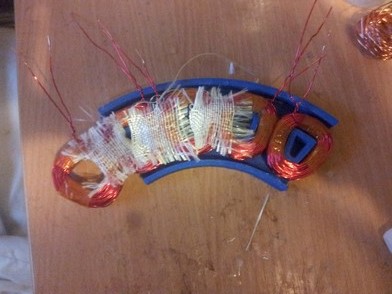
After a while I have all the coils attached together

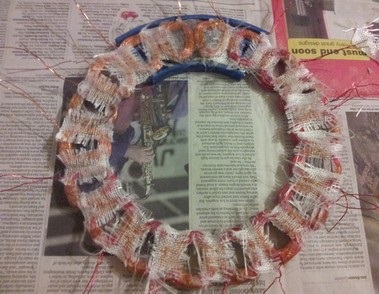
They then go in the mould with strips of newspaper around the outside to wedge them into the right position and keep them there. I used a layer of cling film to make sure I can easily slip the casting out of the mould once set.
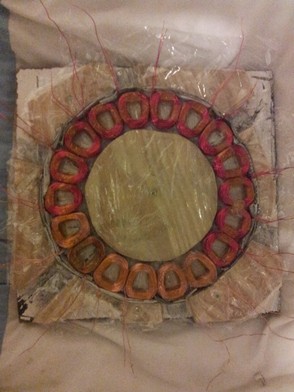
Then I put in the resin with 0.5% hardener added and mixed in thoroughly. The advice from kitestrings on using a syringe to apply the resin was very helpful. The syringe was totally ruined afterwards due to epoxy setting inside it, but they are cheap.
I then placed another layer of cling film and a flat piece of wood on top. Then quite a few bricks to ensure flatness.
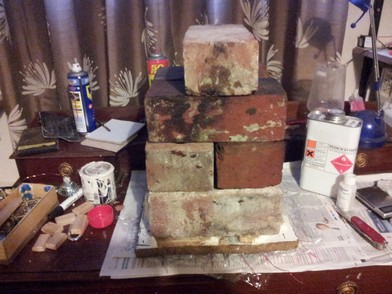
I left it like this overnight and by the next day it was mostly set but still slightly malleable, So I left it for another day. After this it was rock solid but the entire casting had a sticky residue on the outside, maybe this was because the epoxy hadn't entirely set, or maybe it was because I had not mixed it thoroughly enough. Either way, I was not patient enough to wait longer so I removed the residue with acetone. Underneath the residue the casting was fully set and very strong. I think next time I will use something nearer to 0.75% hardener.
Anyway, here I have the completed stator resting on top of the bottom rotor.
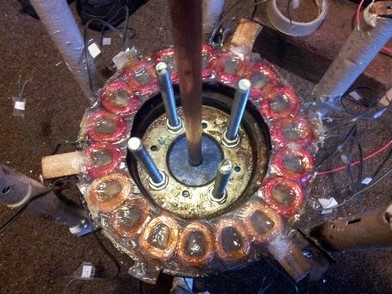
Because I used clear epoxy, I can actually see through the centre of the coils to the magnets underneath, which makes accurately fixing the stator to the frame easier.
I 3d printed four plastic tubes that slide onto the threaded rods and act as spacers. This way I don't have to worry about screwing four nuts up and down threaded rods until the top brake disk is level, I just tighten the nut up to the tube and I know that all four tubes are the same length. I can file down all the tubes equally to reduce my air gap.
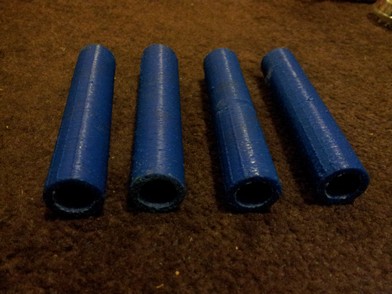
Here is the assembly minus the top brake disk with the tubes spacing the nuts:
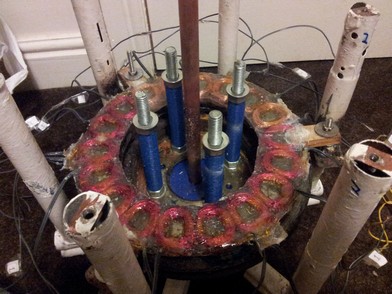
After adding the top brake disk and adjusting everything it's time for some testing.
Open circuit I get 12v at about 130rpm and 18v at about 200rpm.
Short circuit current is about 0.5A, which is the most I can do by hand, above that it gets very difficult to turn. I imagine a bike or windmill would be able to apply much more torque.
I think that the cut in speed is a bit high for a VAWT. What do you guys think? I have enough clearance to reduce my airgap by about another 1mm so I will try that.
But also I think my wiring is non standard. It's not star or delta, I don't even know if this has a name:
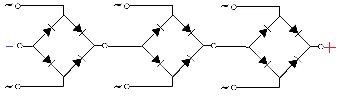
One full wave rectifier for each phase and then each rectifier is connected in series. I did this because I built my 3 phase rectifier a while ago when I was less educated. Is this arrangement inefficient and would re-wiring to star give me a higher voltage? I have the wires exposed for each individual coil so I can play around as much as I want.
Thanks