Big update -
Bending the silicon steel shims turned out to be a large amount of work. 84 shims (7 layers x 12 coils) and 3 bends per shim. First I went to a friend's house to use their sheet metal shear. Next I did the middle bends with just a board and me eyeballing the angle until it matched the previous shim. Then I made a special wood fixture to get the legs of the shims bent to the right angle, which was super challenging since the width of the center and the legs all needed to be correct within about 0.010", else they wouldn't nest into each other properly. This meant there was a lot of tolerance stackup from the original blank piece of steel to the final width. I tried really hard to get them as perfect as possible.
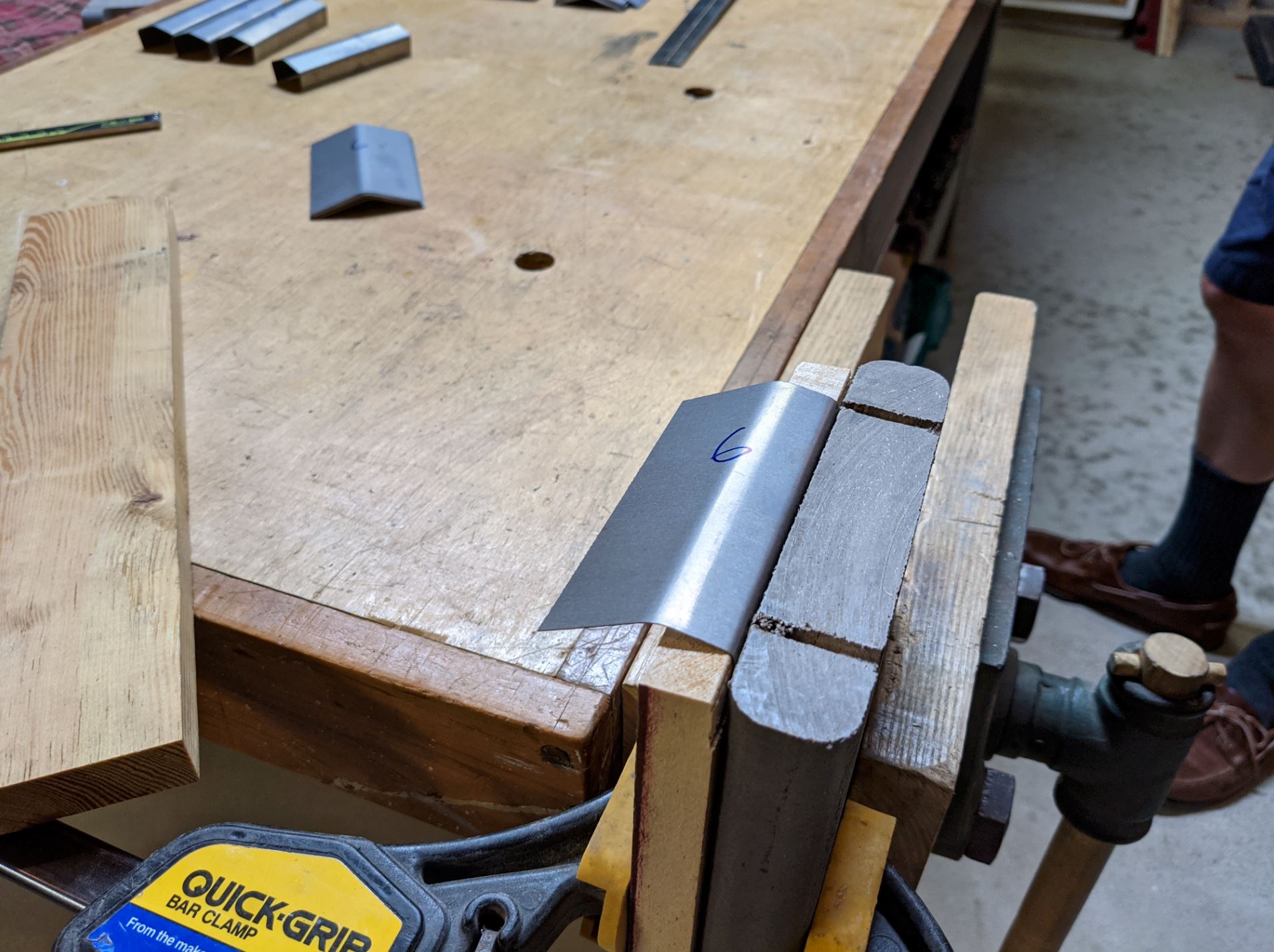
Here's the final line up.
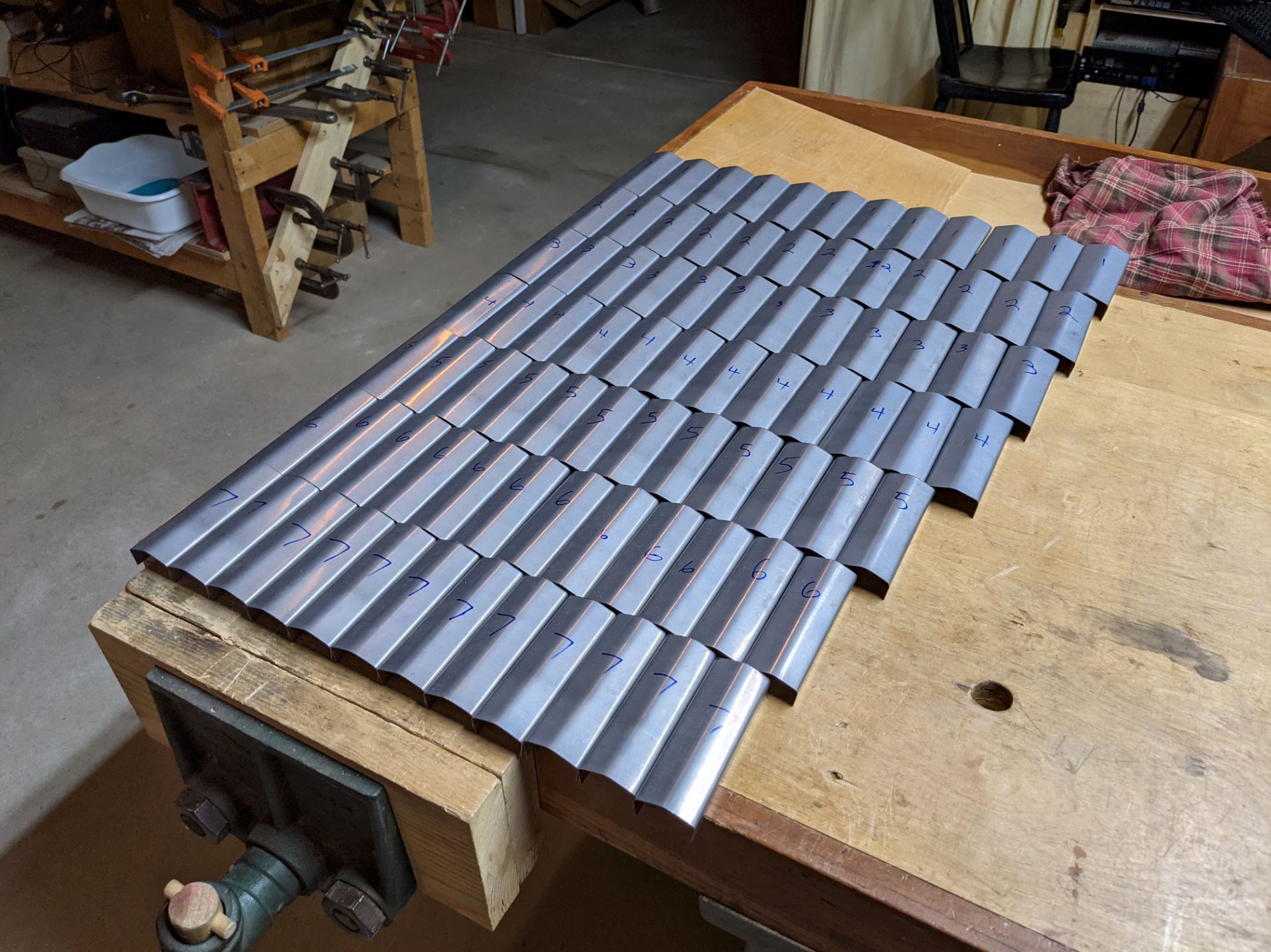
This is after I spray the shims with clear lacquer and then assembled them.

After taking off the zip ties from the wires that held them to the stator, I tied a long 1/4" rope around the whole thing to keep the wires from jumping off. I then took some Gorilla tape and made a 1/4" wide hoop of it on the very outsides of the coils so I could take the rope off. The next step was to add two rows of packaging tape around the center of it and then slice each slot with a razor blade before adding the shims in. I found that all 7 shims weren't going to fit due to the total circumferential stack up around the alternator. Else, the shim legs wouldn't touch the bottom of their slots (think Roman arch with one too many rocks or keystones). I ended up settling on leaving shim numbers 1 and 2 out, for a total of 5.
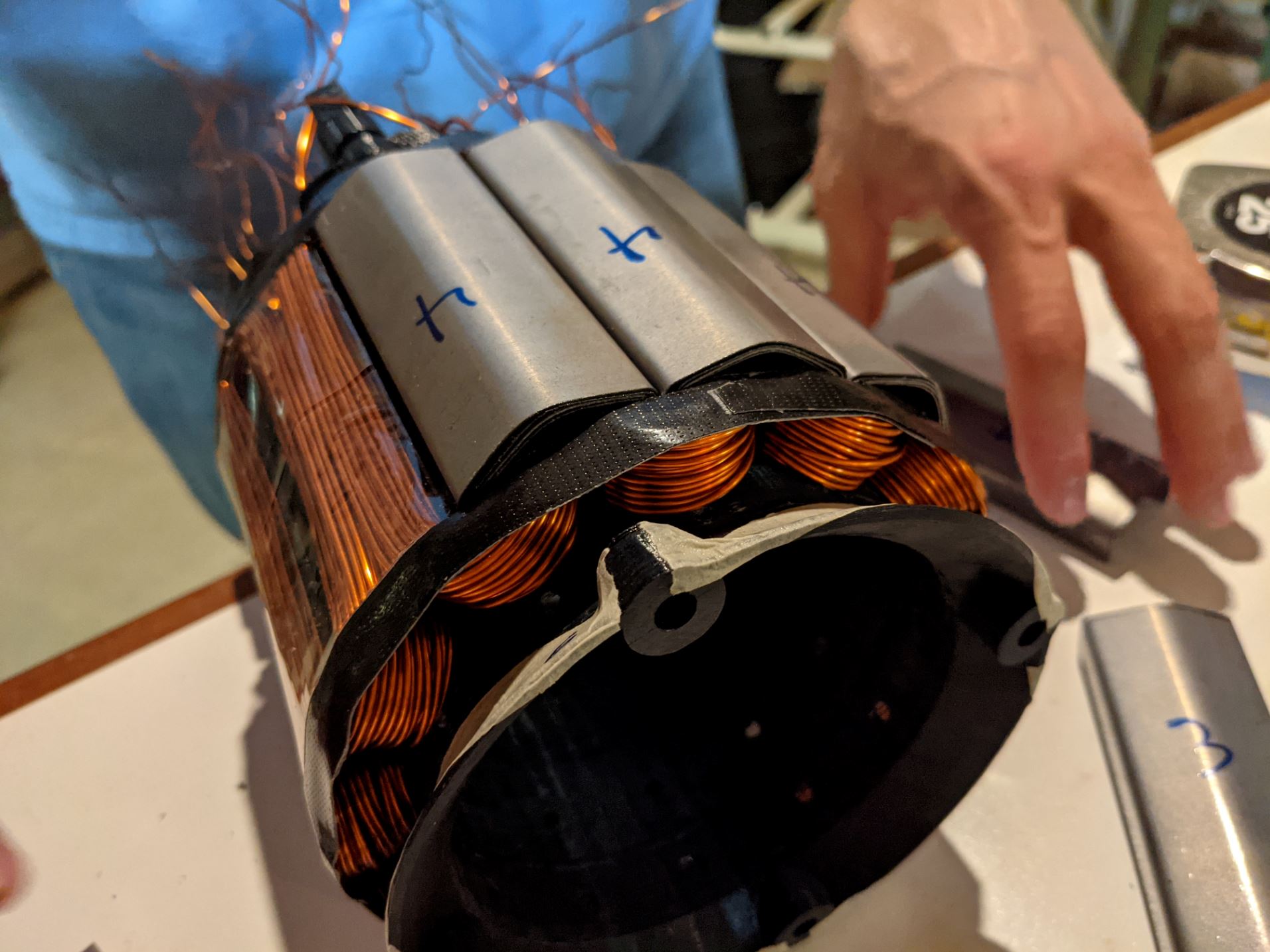

The next challenge was how to squeeze the shims into their final position. I was initially thinking some vinyl coated 1/16" or 1/8" steel cable to wrap around the whole thing, but while at the hardware store, I came across some 24", 175 lb, 85C rated zip ties. 9 of them seemed to do just the trick.

Last night I took a swing at balancing the steel hubs. I put some large washers and 3/8" bolts in the various holes until I balanced it. I spun it up with my RC car battery charger and the original treadmill motor to about 400 rpm. It seems like I was off by about 300 inch*grams (today I'm going to hunt down a food scale to get the accurate number). My blades are off by about 360 inch*grams, so I might get away with just putting the right blade in the right position. We shall see. Spinning the full blade assembly up to speed in my basement is possible, but it has to be solidly mounted to my workbench, which then I can't feel how strong the vibrations are. While on the floor in this photo, it would move around like a floppy fish until I got it balanced.

The next challenge is making sure the magnets don't stick to the inside edge of the stator. My wood test shaft, along with the poor fit with the bearings is letting it move a lot, so it won't spin yet. There is enough clearance, but not much to spare. Once I figure that out, I should be able to test the alternator. I don't think I'll be able to put it in the drill press, but I should be able to put it into the windmill and drive it with the treadmill motor.