I installed the anti-cogging device. It didn't work like I was hoping. It only slightly improved the start up torque (~10% improvement) and it only lasted a day before the cam lobe wore out due to fatigue.

My rather accurate measurement device for measuring start up torque. As you can see, it's pretty bad to stop 16 oz of water at a distance of 40". The cogging rotor dropped that to about 36". Unfortunately, it could be even worse at one spot of the rotation where my magnets were rubbing in my alternator, bumping this up to something closer to 60".
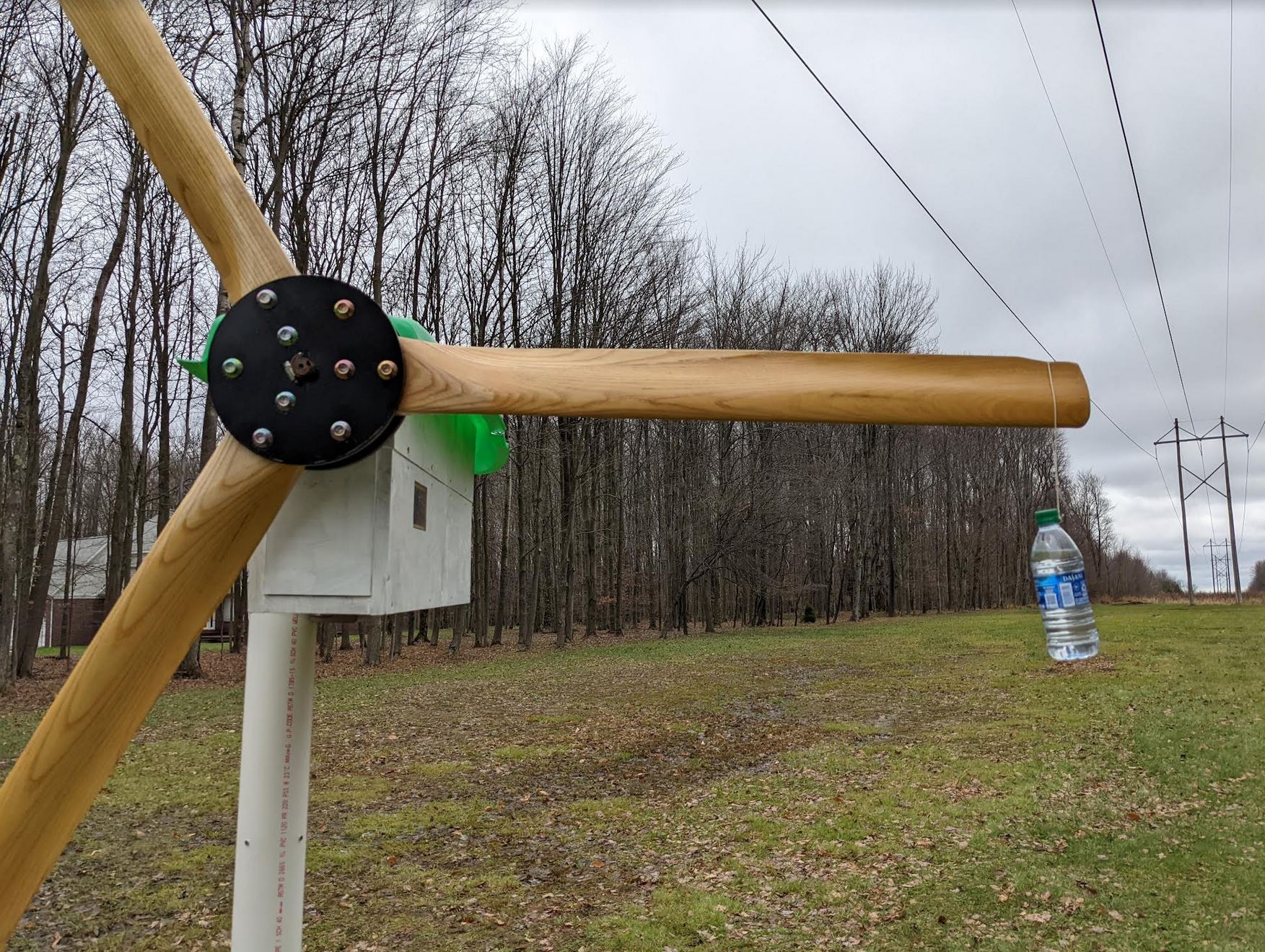
So I did what I didn't want to do and decided to bring the whole thing back inside. It's a real bear to lift it two feet above the top of the tower since it weighs ~ 100 lbs, even with 3 people. I had spent about 8 hours outside the one day on a ladder messing with different things to improve the start up torque, but it ended up not bearing any fruit.
Once inside, I decided it was time to rewire it. So today I drew out my current and new layouts on paper and got to work changing the wires around. It actually turned out to be rather easy. Now all of the coils are in parallel in each phase (12 coils, 3 phase, 4x1 for each phase of 17 gauge, 68 turns).
Before and after wiring it, I did some more thorough bench testing, both with my extra 0.8 ohm resistor in line and without it for the 2x2 configuration and then later with just the 4x1 coil setup. I hooked it up to my new battery I just finished, which is ~1.7 kWh of used 21700 Li-ion cells from a Tesla Model 3. I have hot-swappable plugs so I can change it from 99 cells @ 3.7 volts to 33 x 3 cells at 11.1 volts. So today's testing was done in parallel mode @ ~455 Ah of capacity.
To drive the hub, I used a DeWalt 20v brushless drill (model DCD790) in low range (600 rpm max). DeWalt's website claims it can do 360 watts at the chuck at it's peak RPM/load point... of course they don't list what that RPM is. But at least I have a ball park of what I'm putting into rotor.
I used a GoPro and a piece of tape to record the rotor RPM and my power meter. I then reviewed the footage and went frame by frame to figure out the exact RPM, which was fairly easy to do with a spreadsheet to calculate everything.
So the first piece of data is the peak power into the battery I measured at full throttle on the drill. In the original 2x2 configuration and with the resistor, I measured about 72 watts. With the new 4x1 coil setup, I measured 120 watts. I think this was mostly due to there being less voltage drop across a particular coil (less I^2*R losses) and minorly affected by the drill being able to make more shaft power at the higher RPM. Assuming the drill could actually provide 360 watts, that's a generator + charging circuit efficiency of about 20% vs 33%... which seems reasonable considering what I'm doing with all of this low voltage stuff (20% lost right away in my diode, and some sizeable amount lost due to eddy currents in the shims and another sizeable amount lost in the resistance of the connections and other wiring, and some lost in the 3 phase rectifier).
Here's the amps vs. RPM of the 3 different setups. It follows what I expected. The original data I took a few months ago is also on this plot to show how that it still lines up pretty good with today's testing.

Here's the power vs. rpm. The black dashed line is the new 4x1 coil configuration. The lighter thin solid lines are the older 2x2 and 2x2 + the 0.8 ohm resistor lines.
The colored curved lines are scaled values to compare the power available from the blades depending on the multiplier for the generator efficiency and the efficiency of the blades.
This makes it readily apparent that the old setup was never going to work since the generator was even less efficient and the blades never made enough power to match the generator.
The new setup appears that it might just work and spin up to a decent speed so the blades can kick in.
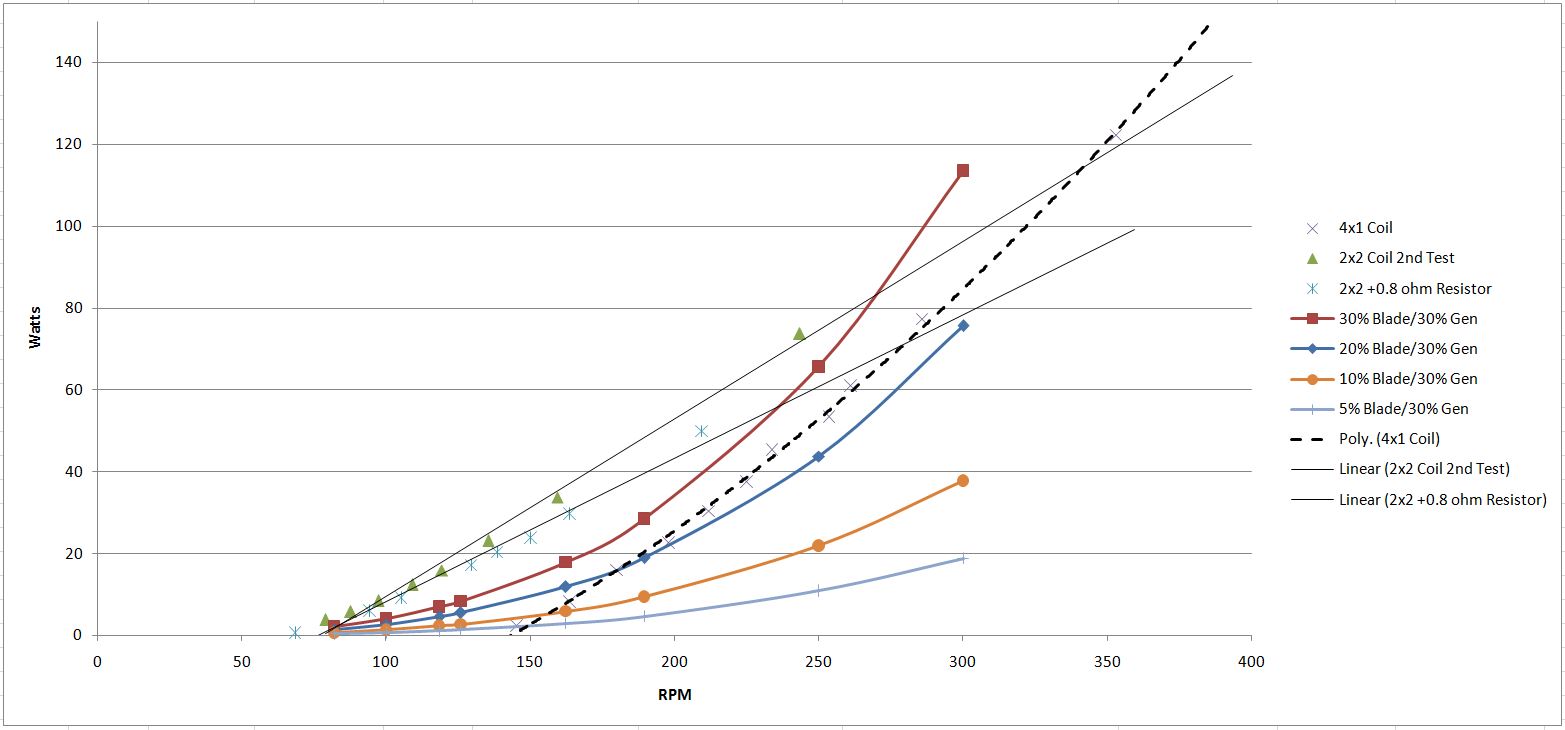
To further bring home this point, here's the calculated blade efficiency required assuming a constant TSR of 4. Obviously this isn't going to happen in real life, but having a lower value will help.
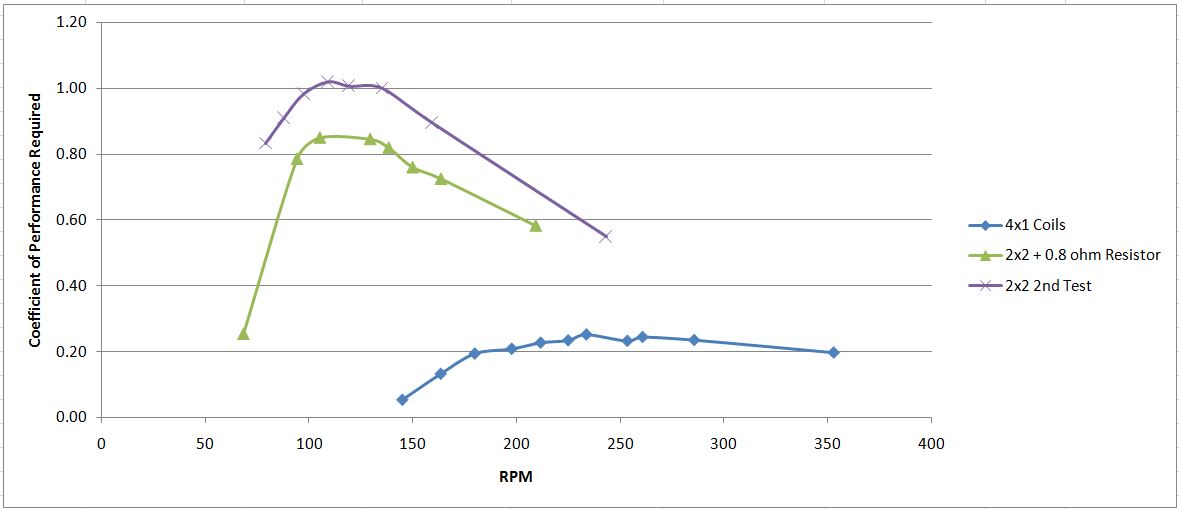
So, what's next?
Well, I still need to fix the start up problem. After a bunch of thought and my desire to keep things easy and reliable, I think my leading choice is making a dog clutch and governor to control the power going to the shaft. I would mount it on the front of the hub and then put ball bearings in the two steel discs. Then the blades can rotate super freely until the RPM gets high enough to engage. I would probably have it kick in at 180-200 rpm if I can get away with it.
Other options aren't as easy. Like having a viscous coupling to bleed off a few RPM... but this would be a serious engineering project on many levels. Another option is to break the shaft in two, push the alternator back and have an electric PTO clutch. The down side would be the power consumption from the electronics to make this happen and the tuning of such a device. The third option is to have a motor on the shaft to kick start it when the wind picked up, but that requires yet again more electronics and power consumption.