Hi Bruce,
Lead is heavy, and soon jumped upon by the Clockmakers of Europe in the mid 1600's.
By the 1730's most houses with a longcase clock wanted style, so the ugly lead was encased with a thin brass covering that then acted as a tube to poor molten lead into. I still make special weights, for instance for a 2 month regulator design of mine that requires a 12kg one. Just for you Bruce, See photo below, 2 month precision regulator for one of my clients.
On substance we want a weight to be as heavy as possible but yet as small as possible. I did look at and i specified on the UK's Millennium clock was depleted uranium as its nearly as heavy as Gold, which in the early 1980's was available from British Nuclear Fuels. And at a meeting their scientists assured us that as long as we encased it there were no issues, obvious they were desperate to find a market even just for us clockmakers. I wasn't ready at the time. But by 2000 the folk making my Millennium clock kicked up a stink about the clocks weights. I believe the military were using depleted uranium in their bullets and it got withdrawn from the arsenal of weapons it could kill someone .
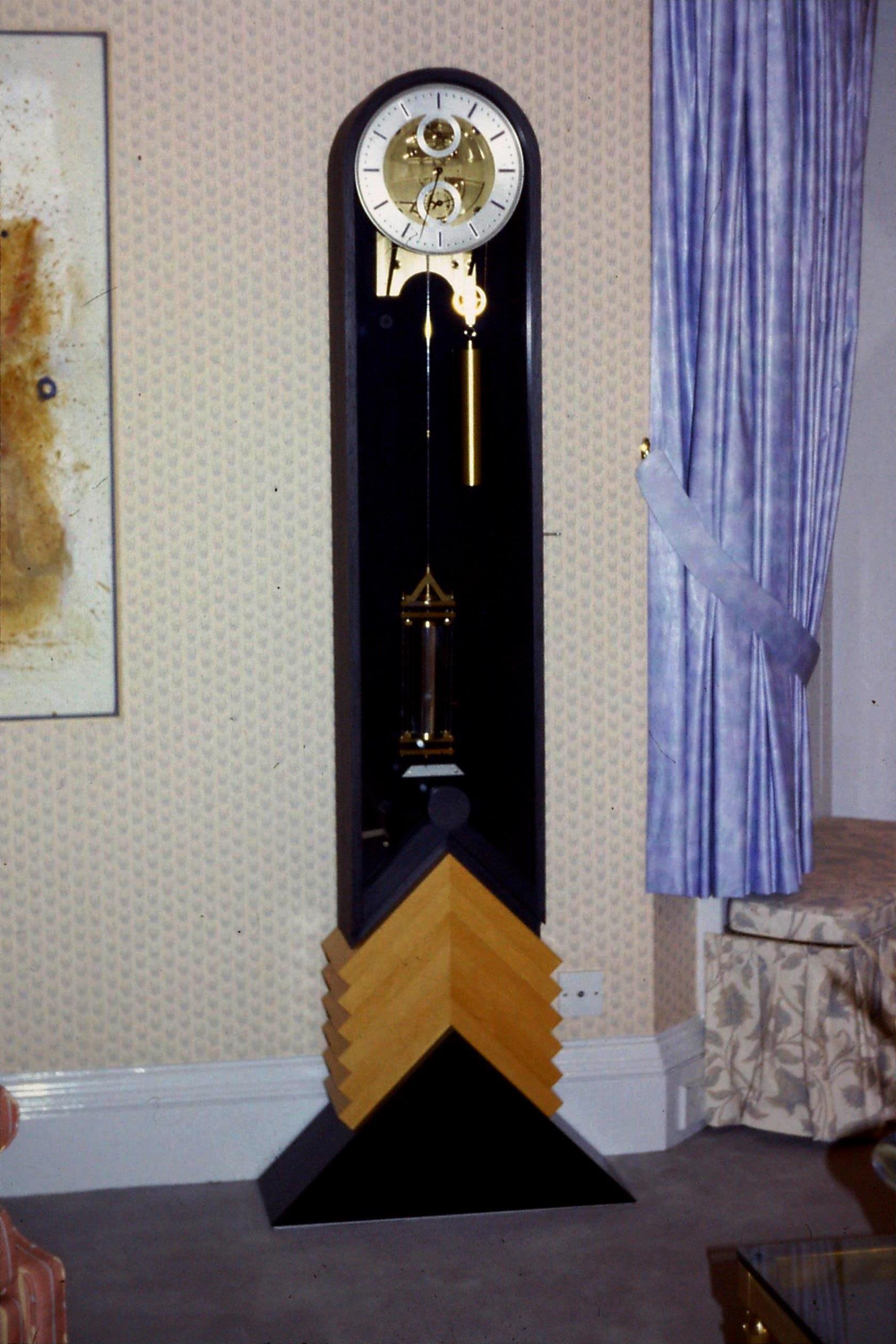
Mary,
Yes something is definitely in that lead from my friends bullets, i know he did his own casting, but his stuff is so dense the only place i could use it was balancing my wind turbine blades with a couple of holes drilled through it.
SparWeb,
You are very correct, finding a supplier that can guarantee lead sheet specifications is not easy. I have 2 in the UK so far. And as you say best to buy in bulk and batches that are known specs. Sadly my recourses are minimum for stock of materials, but i have enough and at good specs to manufacture a couple at least.
As regards EN & ISO etc norms, well like you say its great but open to interpretation. I once had to go on TV as a specialist qualified representative of the Clock & Watch Institutions, regards Water Proof and Water Resistance Watches. ISO rules and documents were so wishy washy that most Companies were driving a Coach and Horses through them. I was ready, I had taken 10 watches recently on the market from a Sports Clothing Brand and put them all through ISO testing standards, and yes all on TV, and yes most failed, but on the dials etc it had written 20 meters etc, but in-fact only splash proof. That's a Brand that hates me. LOL.
SparWeb sometime over a few beers i will tell you the whole story, still makes me chuckle when i think of it, I was always white shirt, but open neck no cravat/tie and always asking "what you going to ask me". Acting on behalf of professional organisations i never wanted to be a bumbling old professor type.
I had to do the interview on the back of a Luxury motor yacht in a posh mariner, and the Models were going to jump into the sea with the watches on, however when it came to Live broadcast the tide had gone out and the models had to pretend to jump into the sea. I struggled to keep a straight face as things slowly went down hill from there. I was told by friends that i held up well and very professional, yea right. I did a few more TV stuff after that.
joestue,
I am giving the PLANTE design of solid lead plates a modern twist.
To increase the oxidation of the plates to form the correct type of Oxide that will improve the battery ah capacity, each plate will receive 0.5 deep and 0.5mm wide and 0.5mm between each, scoured into the lead plate with a a comb. And then by charging and discharging and each time reversing the positive and negative polarity, a good Oxide will build up a bit quicker with out making the lead sheet to thin, and so still support it self for the next 30 years or so.
After due consideration, the comb is best achieved using a cat and dog FLEE comb which must be stainless steel as we do not want any bits of iron getting stuck in the lead. So every day Flee combs keep arriving in the post for me to test. Remember this whole process of making PLANTE batteries is for normal folk to make and keep a standard of production.