Hello again!
I have updated my plan during past couple months.
I am increasing Blade diameter to 4.2 meters from Hugh's book and rotor size also to either 400mm or 450mm.
I sourced some free 1.6mm diameter electrical wire to mock-up coil shapes/sizes for given rotor size and based on results did some maths.
I can fit 114 turns into a rectangular shaped coil when using 400mm rotor disk which according to my calculations would output 50volts DC @ 95 RPM according to this formula
(A x B x n x rpm x 2,7/30)-1,4.I also tried to calculate at what m/s wind speed the turbine would reach 95 RPM, by using this formula > ((2xPIxradius)/60)*RPM which gave me
~2m/s, but that doesn't seem right...
I also spun a triangular shaped coil, 120 turns, with room for at least another 10-15 turns. So lets say 130 turns for triangular coils: 57,2872, but there would be losses due to not all flux linking, but i dont know how to calculate those losses.
Now obviously i could fit quite a bit more copper into coils if i used the 450mm rotors, but should i? At which points is the cut-in rpm too low that will cause stalling issues?
Heres a few pics of my mockup coils:
114 turns square coil on 400mm rotor:
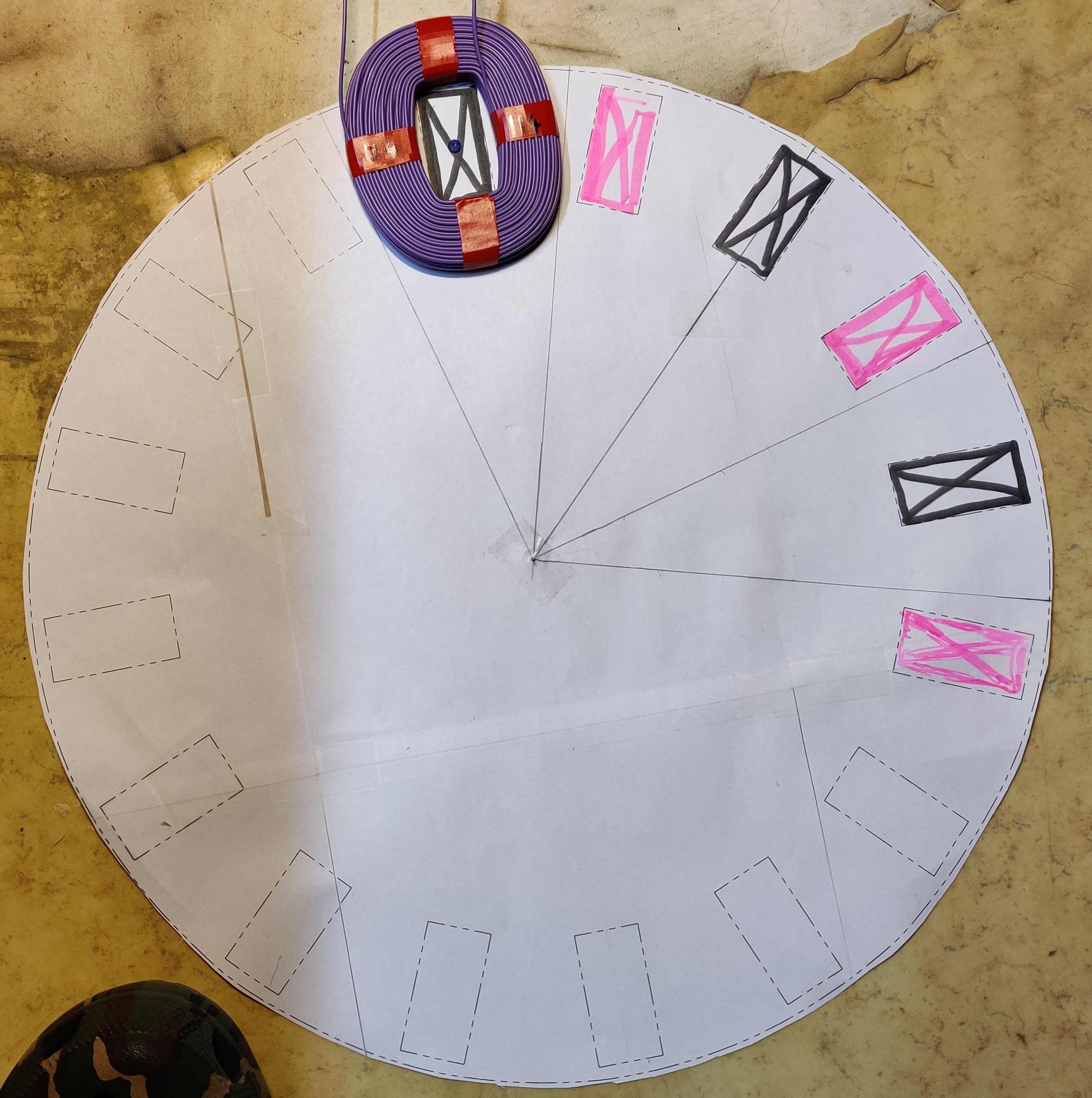
114 turns square coil on 450mm rotor:( ignore incorrect amonut of magnets on the 450mm diameter, i did an oopsie in Fusion 360, didnt want to reprint

)
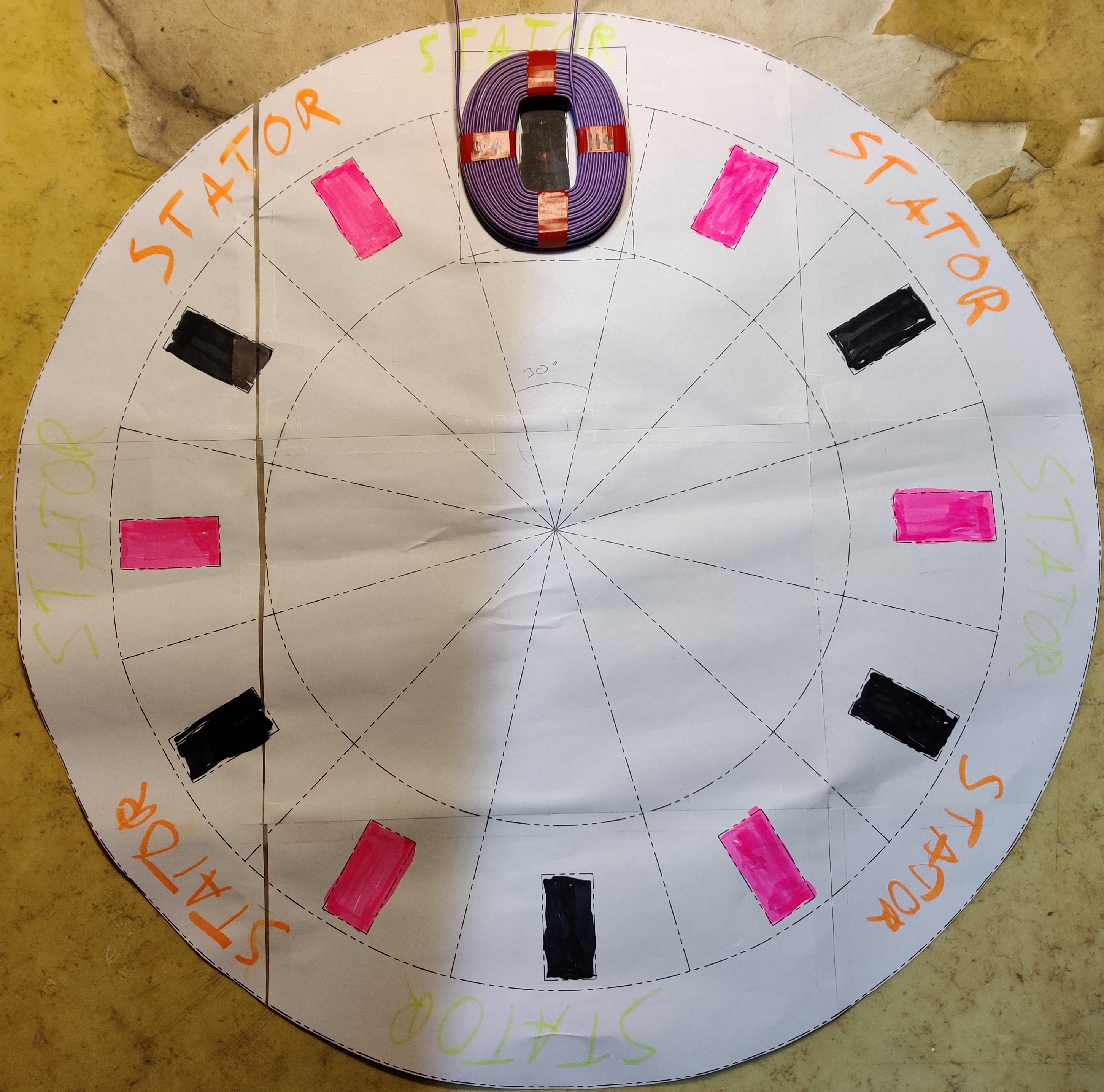
120 turns triangle coil on 400mm rotor:
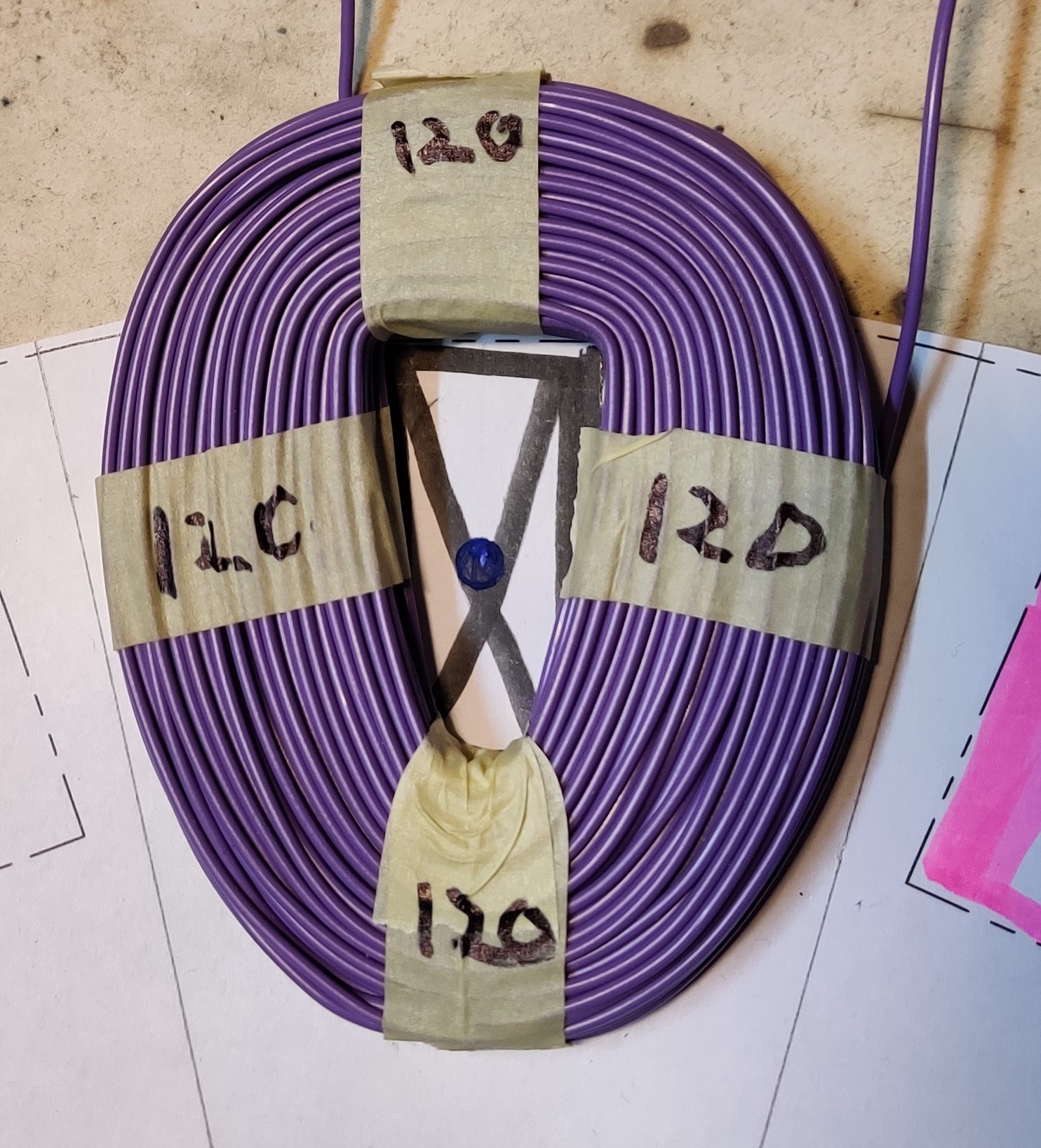
120 turns triangle coil on 450mm rotor:
