G'Day Guy's,
Well it has been awhile since I updated this post so here we go....
I had a thought on how to regulate the RPM and came up with a concept drawing for a variable drive
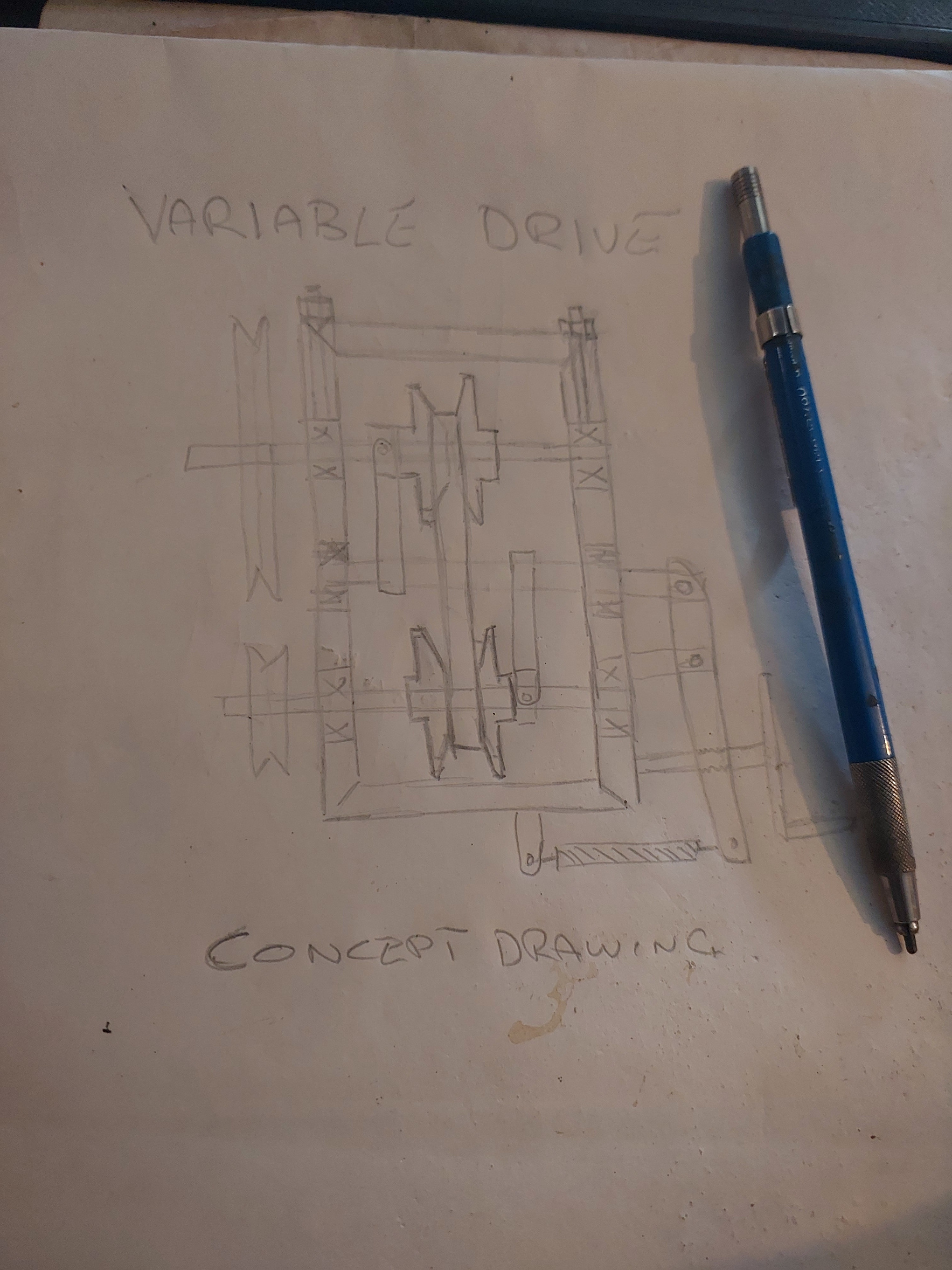
So as one can see the centre shaft regulates the speed and I have started to make the pattern of the disks so I can get them cast so the normalizing can start after I rough machine the castings.
Started a new job and got told see those packs of 6" pipe well they are offcuts ( insert Shocked emoji) plenty of larger pipe there so the design for the tower is going to come together. I'm thinking with the pipe length being 3 metres of welding 3 sections and welding in bracing on the joints where the above joint can be a section for mounting the guy wires.
So the gin pole will be the same 6" section and same length so I can just use my tractor to raise and lower the tower.
Now for the smarts for this project I will be making a circuit board with a pic32 as the brain and I'll program MMBasic in it so the programming will be done in Basic where talking it out with the girls can figure out the master plan then I can tech the girls just how to write a basic program.
There is still one task to sort out and thats the wire run and my thoughts of using 400 amp welding cable may be a tad over board so my question is for bringing down around 3Kw of wild AC what cable is the best.
Another task to solve is setting up a prony brake when I do the test and I'm thinking as this is a flange mount motor a solid coupling could hold the weight then a prony brake can be setup BUT as I've only read about this method some guidance will be needed as getting all the data is needed to establish the blade length and profile. I am thinking Sparweb is a guru at this and provide some info on doing this practice as this is something I do want to learn, back in the day when I was doing that engineers degree only to find doing shutdowns was the go I didn't get the learning for that theory.
My goal is get this in the air and finished so I can start the next one using a larger donor motor and get the magnets soon before the China bubble bursts.
Cheers Bryan