The primary idea would be to place it on top of the turbine, so I'm very concerned that the weight doesn't go too high. Weight control is not just a whim. Because when I lift the column (which during the assembly will be horizontal a few meters from the ground) the lever that can make an excessive weight on the tip can complicate the tasks of lifting the column.
But if I can't get the correct rpm in the generator for the power of the turbine (for that I want to play with 6 rectifiers, 2 per stator) I'm going to be forced to place it below and adapt a transmission with helical nylon gears, until achieve the most suitable transmission for the power of the turbine at the desired wind speed.
Today i tested the prototype with the comercial 48v-800w PMG, i used a planetary gearbox 5-1 to give the increase in rpm to the PMG. Those multipliers are delicate and inefficient, but it's easy to swap one for the other and try different ratios, so I chose them for testing.
I really didn't feel like taking the turbine to the coast, it's 300 meters and it's summer here and a spa, it's full of people on the boulevard and many of them stop to ask you what you're testing, and they run the risk of have an accident with so much traffic.
So I went to a couple of squares that face my house, where there are hardly any trees within a radius of 80 meters, and I hoped to find at least some of the wind that I know was on the coast today.
In the end the wind speed was quite disappointing, 4 to 8 k/h and very short gusts (1 or 2 seconds long) from 10 to 14 k/h.
But at least I was able to verify that this relation of transmission does not correspond to the turbine, because it never stopped turning even when the wind dropped to 2 or 3 kph under load.
That gave me the reference that you need a slightly higher transmission, perhaps 8 turns to 1 to force the generator a little more to deliver current in very light winds (it barely delivered 7 or 8 watts at the current speed) and only 40v without load.
I remember trying that same generator but with a self-starting crown gear drive, and a ratio of 15 to 1, and it was too high, it barely allowed the turbine to turn with load, and without load it would pick up 140 volts with a wind of 14 km/h.
So the ideal point for that turbine size must be around 8 to 1, and I don't have planetary transmissions in that range, I have 5 to 1, 13 to 1 and 18 to 1. And those last two are extremely inefficient due to the cascade of gears to reach those multiplications.
That is why I think it will be quite a challenge for the turbine to reach the best rpm ratio with respect to the different torques that it can regulate (they are modest but the differences in torque are noticeable between one type of connection and the other) by changing the connections between stators from parallel to series.
I don't think it will pick up more than 35-40 rpms in the target wind of about 16-18k/h. So I think that the coils could not have wire larger than 1mm to ensure that I will have some resistance to cutting at those VERY low rpms.
And in the event that it does not reach the necessary rpms to obtain useful current, I am going to be forced to use a gearbox, so all the investment in achieving a PMG for very low rpms will be a bit meaningless, but if not you try you will never know.
I made a very basic drawing in corel draw simulating a 3d view of the way the E would be placed on the stators and the steel disc that would hold them, it can help those who are interested in the thread but do not understand how to use it the E to assemble the rotor.
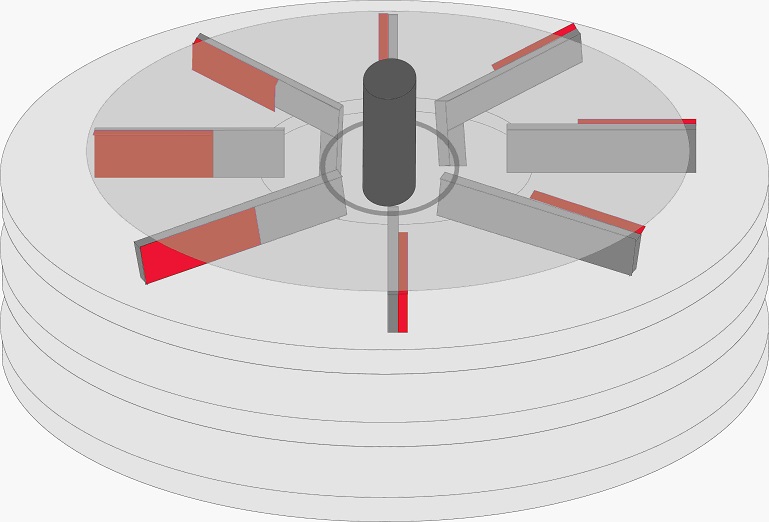
The draw have only 8 poles, i dont had will to draw the complete 16 without a easy program to do that.
https://youtube.com/shorts/rOSm4ZdeydU?feature=share short video of the test today in the afternoon, without load. With load at that low wind speed it barely reached 7 or 8 watts at 10v, which was the connection voltage of the leds.
I am going to order a planetary transmission from 8 to 1 to see if it improves the load a bit, because it would be more than 50% more rpm than the generator would be subjected to with the same torque, because I don't need it to rotate with winds of 3 k/h without generating almost nothing, it is attractive to see it rotate in such a light breeze, but when it takes a real wind of about 20K/h, the turbine will surely speed up a lot and not deliver all its energy to the PMG axis.