Hi everyone. I'm mostly looking for someone who has tried this concept before. Because of many simpler things there are all possible variations. but this multirotor i have in mind i couldn't find anything similar.
I am already on the way to manufacturing three-blade savonius (I understand that many accept or believe, based on previous studies carried out in wind tunnels and on a small scale, that 2-blade designs are more efficient, but in my case I made several small-scale prototypes and the one that I find it more efficient is the 3-blade one.
In any case, the difference between the efficiency of one model and the other is not crazy either. If we decide to go for savonius it is because the other systems depending on the ideal location and stable winds are not an option (like darrieus design).
The problem I find with the savonius is its low TSR, but its huge torque in very low wind speeds makes up for it.
So the way to compensate for that is to use very low rpm generators that don't rely so much on a high ratio transmission that it wastes too much kinetic energy in the conversion.
And the bigger the savonius, the slower it rotates at the same wind speed compared to narrower models.
So manufacturing a suitable axial generator is the big question.
As I am a fan of wind turbines thing since my 20's I have read and studied and watched videos of all things related for many years. And based on all that is that I have defined how to make my turbine model.
But for what is the design of the generator taking into consideration the low rpm that I need ideally, the axial coreless and multirotor is the most adequate.
And here is the beginning of the matter. Multirotors with steel discs in each series of magnets are not attractive to me due to excessive weight and risk of accidents during assembly. In addition to massively using nodymium magnets, which is the most expensive part of the set.
So I came to the conclusion that the best arrangement is to put my magnets upright, and make their magnetization different from the conventional one.
In this way, with 4 rows of magnets I can drive 3 stators. Of course, with less intensity than if you put a single stator and two iron discs, but with sufficient flux density, and even for the two external rotors of the set, these two can be mounted on two iron discs to support the set.
And i can imagine that using double layer winding on each stator and connecting in series the outputs of the rectifiers i could get a very good voltage at very low rpm, and with the massive amount of stators and the 20mm gap between the rotors i wouldn't suffer from overheating excessive of the set for an average power of 400 watts of output.
thats is the image with only a layer of coils, would be two layers to cover more surface of the disc with copper. 7mm tick each layer of coils. around 15-16mm tick the whole stator.
The generator will have massive quantitys of copper ,and massive quantity of magnets.
With that in mind I'm hoping to get the generator to put out at least 14-15 volts at 60 rpm. And about 300 watts. ( i can play with the conections at the exit of rectificators betwen the stators to reach the more adecuate voltaje and current).
It is necessary to clarify that I have in my possession 2 radial commercial type generators, with 600 watts of power at 500 rpm, one is for 12v the other for 48v, and although they are quite adjusted to the power marked by the manufacturer, I could not make a transmission that will take me from 60 rpm to 500 without losing much rotor energy in speed conversion. And that also those alternators probably would cook on the first stormy day (actually inclusive i am only using a couple of hoverboards in paralel for to do the tests in the prototype) That's why I'm going to play with an oversized alternator to make sure it doesn't overheat too much on stormy days.
The turbine will have around 4.8 meters in height, 3.14 meters in wide. I have a prototype at scale, of 2.2meters x1.7 meters and gave 70-80 watts in 20k/h wind. That is enough results for me to try the jump in scale for a more reasonable use of real generation.
But because I am defining the parameters of the aluminum E to be machined in China (I am making all the components in China to order) and seeing that in this forum they have made very crazy ideas and not so much all kinds of generators. Maybe someone in the past tried to do something similar to this generator concept and failed in X issue and it would be nice to know to correct before investing thousands of dollars in parts that eventually would not work as expected.
Only in magnets I already have to spend 2000 dollars to have enough magnets for 3 generators. So it scares me a lot not to be considering something that maybe someone already tried before and for X reasons it didn't work.
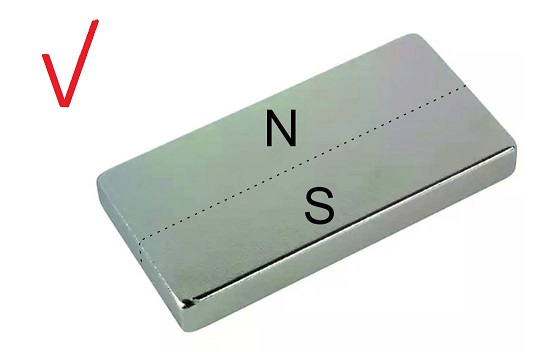
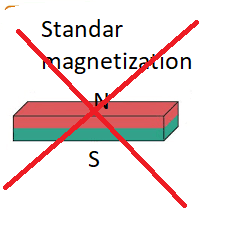
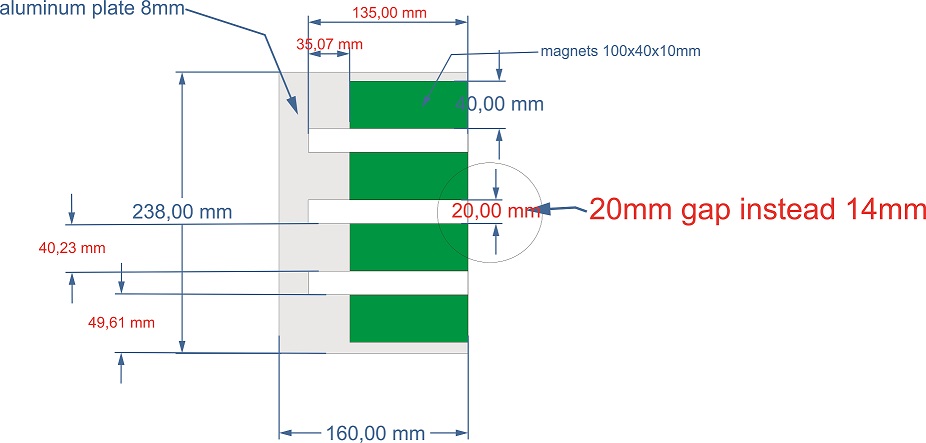
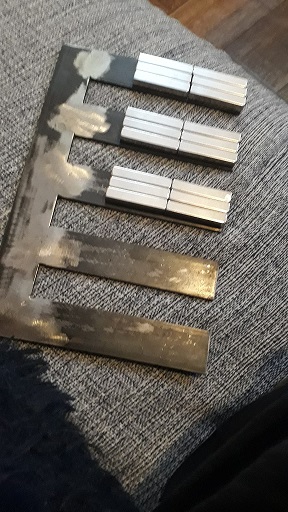
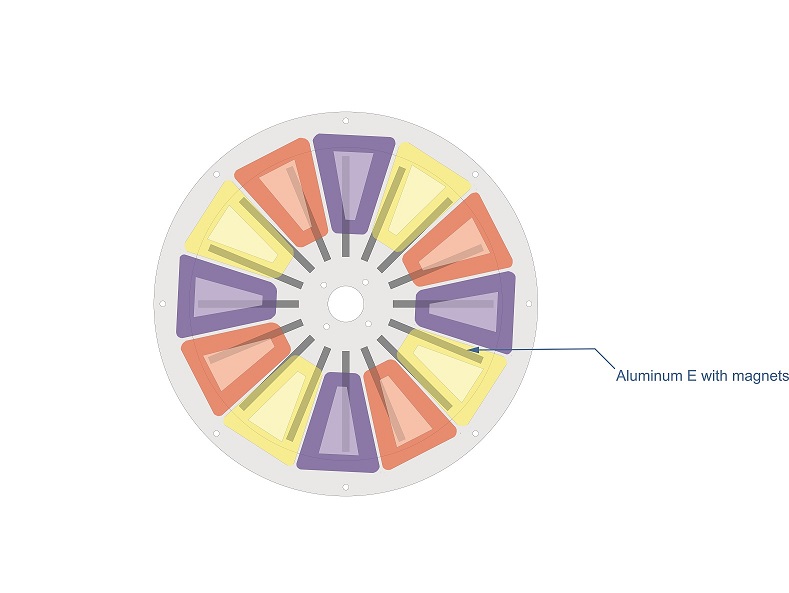