About a dozen years ago I created an accidental hybrid between a HAWT and a VAWT, where the blade moved along a sloped plane rather than horizontal or vertical. I've been thinking about it ever since. It seems plausible to actually get the drag from the blade moving in all 360 degrees of rotation if my thoughts are correct. While not as fast rotating as a HAWT, I found the original to rotate quite a bit faster than a VAWT. The concept should work both as a wide/skinny blade or as short/fat, although the raw RPMs will not be equal.
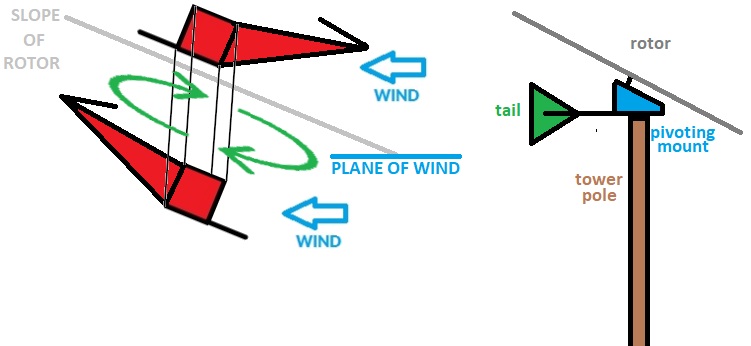
The original was only about 8 feet off the ground and would spin at speeds the HAWTs wouldn't even register wind. It is directional, but with a slight offset between the pivot of the tower and rotor, it needs minimal tail. The tail is really for stability to slow down its twitchy behavior, because it wants to instantly turn towards the wind origin.
The front stroke, is moving with the wind, so in essence its kind of a back stroke I guess. The arm begins the stroke at the front dead center, so I'll refer to it as the front stroke. There are two key points of drag on the front stroke: (1) the rear L channel, and (2) the nose V channel. The air flow smoothly follows these channels from the tip to the center of the rotor for 90 degrees, then reverses to flow from rotor center to tip for the second 90 degrees. The idea is not to truly stop the wind behind the blade, but rather to allow it to follow the channels. Probably doesn't make a difference, but its a curious flow pattern. Other designs seem to be better off when not blocking off air flow through the design.
The return stroke, in contrast, begins at back dead center and is generally moving into the wind. I've been thinking that the front of the blade should really have a slight pitch up from the main arm of the blade, to give it minimal air resistance on the return stroke. On the return stroke it actually continues to get pushed forward due to the wind deflection, like a sailboat would tack to move upwind. My original project had a straight blade that worked extremely well, but it could have been better if it tacked. Tipping the slope a bit more than the slope of the blade may enhance both strokes, but add drag in the return slope, so not sure it would add any advantage.
The original design had three arms. There should be minimal interference from disturbed air between arms, so 6 arms could realistically work. More arms would increase the weight, so 3 is optimal IMHO.
What are the opinions about this idea?