I've been going over and over the last few days about the design of the savonius blades.
As the savonius has some effect lift at a certain angle of its turn, it is possible to think that the returning blade is not ALL the time making drag force.
But if at least 30-40% of the time (and that is if the design allows for some elevation effect)
Considering that and that the drag effect is the product of the square of the velocity, a Savonius turbine rotating at 0.9 TSR in a 16 k/h wind has a blade tip speed of 14.4 k/h.
But here comes the detail... the one that returns adds those 14.4 k/h to the 16k/h of the wind speed.
That means about 30 km/h for the returning blade.
Now let's suppose that the blade has a semi-clindrical shape that gives us a drag coefficient of 0.38 to 0.60 according to the tables (the measurements vary a little depending on which tables you consult and the curve ratio)
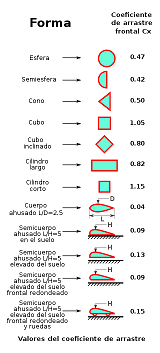
So the count would be 0.38x the square of the velocity that is 30x30x0.38= 342
From this account we would have to subtract the moment in which the angle of the blade causes suction and that the curve of the blade is not perpendicular to the wind all the time. So that drag effect could go down by 40-50% (that improvement is my assumption, it could be something more or something less).
Then we could assume that the drag coefficient is only 200 in that wind speed.
While the positive drag would be the product of the wind speed by the drag coefficient of that same semicircle: 1.42x the square of 16k/h= 363.
This is assuming that the blade is going to exert positive pressure in the turn from 0 to 180 degrees of turn, from less to more.
So the positive torque difference would be the product of 363- 200= 163.
That is what you can extract from drag difference: 60% being extremely positive in the calculations.
Probably the difference in torques is not so large, those calculations are thinking of the best of all worlds, and of the best two-blade savonius.
But I do these accounts simply to take as a basis for what I want to do now.
As seen in the second table, the drag coefficient of a teardrop profile is 0.04 drag, against 0.38 for a semicircular profile.
Achieving that exact profile in a normal savonius blade is not possible, because it would be more like a darrieus.
But the drag coefficient could be lowered by making a much more stylized blade curve, without reaching the extreme of the lenz design, which could take some advantage of the darrieus system, but loses almost all the drag that a savonius can generate in light and moderate winds (Until today I only saw one model of lenz working in very light winds, but without load, when not....).
For this reason and taking into account that I have to wait almost a month for the magnet samples to arrive and to be able to continue with the rotor tests, I decided to try a new blade shape for my savonius. At least in the small prototype. I already have the polypropylene plates and aluminum profiles that I had already bought for months in my last import, so the costs of testing this new design will be very modest.
According to my calculations, if I manage to lower the drag coefficient from 0.38 to 0.15 (very conservative considering that the tear has 0.04) I could do the drag multiplication in this way 0.15x the square of 30K/h = 135
And if I subtract 50% from that (as in the previous calculation) in concept of suction moment and the angles in which it does not face the wind at 90 degrees, it could reach 65 of drag, which would leave me a potential difference in torque of 300 instead the 163 in normal savonius shape of blades.
It would be twice what I get now from positive torque, the only drawback I find is that with the same amount of material for the blades, the total diameter decreases by 30%. So the swept area decreases a little bit.
This would be the new shape of the blades. And turning the drawing in corel, I think that almost at no time is the leading edge facing 100% perpendicular to the wind, because what I would expect is very low levels of drag.
If anyone has read this far (I already look like Adrian with the formulas

) I ask them if they have already seen a turbine with a similar design and that at least works.
Maybe someone has already seen something like this, and it saves me from wasting time doing the blades like this to see if it improves performance.
[ Specified attachment is not available ] [ Specified attachment is not available ] [ Specified attachment is not available ]