Hi Seniors and Mentors,
Date: 20/12/2005
My 8.6 ft dual rotor genny has been up atop the 52 ft tower since 20-11-2005 and it is generating just a little short of my daily needs. I have been very involved in ironing out many (off times me-self generated) bugs to get it working as I read you guys seem to have done so effortlessly. Now thinking back I am quite amused how dumb I can be at times.
The first mistake I made, I raise it with the Shorting switch turned on and it took me 4 good days of seeing the genny not moving in gentle winds up to 5 mph before I thought of it. Even posted in the board for help. My first thought was that my 8.6 ft blades are not matched to my 12 inch 24 mags genny since all those in the board are using 10 to 12 ft blades.
Second blunder I forgot to balance the blades completely and had to lower the tower to balance it both for static and dynamic imbalance since one blade tip was too far forward compared to the other two. I had to use 200 grams plus three ½ inch nuts on one allthread to balance the static imbalance. Now it starts easily and pick up speed when the wind catches it.
Third after it has been balanced and more responsive to wind energy I found it was not charging the batteries even though there was increasing voltage with increasing wind speed measured just after the rectifiers going up to 15 V. Once I even saw the ammeter showing 6 amps. I finally traced it after a week of agonizing to the sets of diodes I put just before my 2 batteries to prevent communication between them. With the added diode preload, this low wind period was just not enough to charge the batteries. Now it has been removed and the 6 - 35 amp rectifiers divided into 2 sets of 3 going into the Batteries separately it is finally charging but not equally. The battery that is connected with shorter wire (1/2 the length of the other and half the thickness) seems to get more charge.
The northeast monsoon has finally started to show its dominance and I will be slowly trying to adjust the supply wire resistance by varying the length till both batteries gets more even power supply. If any one has a short cut to get this done I would really appreciate suggestions rather than doing it empirically (trial and error). I am still waiting to see the blades spin till blur so no hope of seeing furling anytime soon. Maybe when the monsoon really rears its ugly head one day. Also I seemed to have over killed my measures to control high wind damage with my mechanical brake system activated by the furling tail. I really don't see the need for it now I realize being inland my area wind speed is actually just marginally enough.
Date: 23/02/06
Spent the last 2 months trying to get enough power out of my wind system. I was convinced I had stall and posted on the board and received sensible help. Finally shorted the wire length back to original, as Flux suggested and found there was no stall at all. All my problems are due to poor turbulent wind conditions in my farm. Cut down some offending trees and now the monsoon is stronger I am getting barely enough power for my daily requirements. I am making a set of 6 feet blades to harvest more power in low and sporadic winds. Going back to the board to read up on blade design for higher speed in low 5mph winds. I understand at the same wind speed, a bigger diameter propeller will have stronger torque but lower rpm. If so I wonder how best to solve this as I need both torque and rotor speed (rpm) in poor winds. I intend to close the air gap to get more flux and more power with the 12 feet prop. Anyway here are my long due photos of my wind system.

There I stand proudly with my coming frustrations for 3 months. The branches on the left are from the durian tree I cut down in Jan 06 to improve the wind available. It is blocking the wind from northeast direction
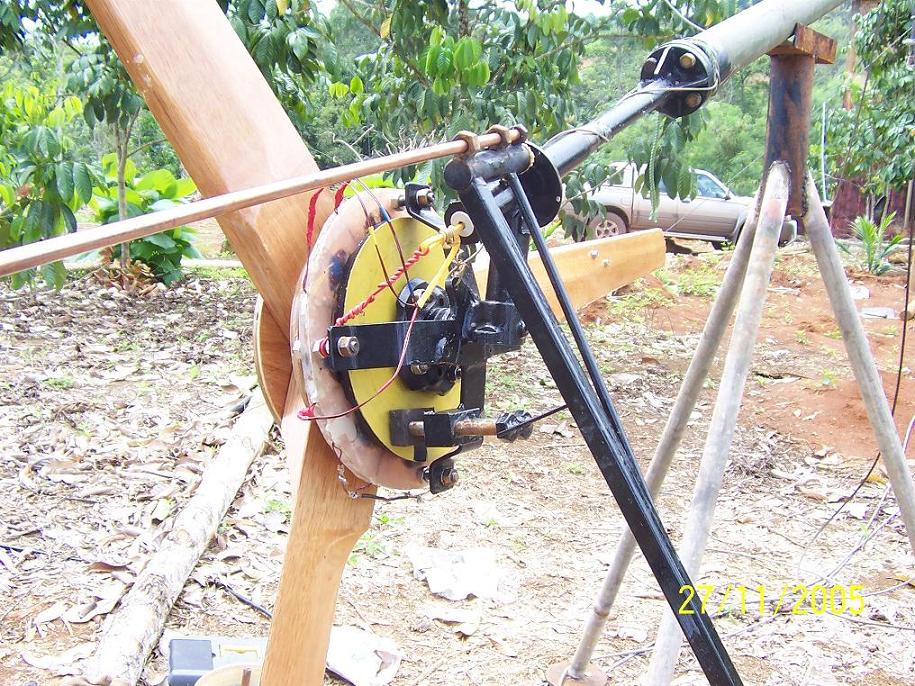
You can see on the lower part of the back magnet rotor my mechanical brake which will come to play when it furls fully. The stronger the wind the harder the brake force applied by the furling tail. A spring between the two plunger rods releases the brake pad contact when the tail unfurls. The brake pad is made from tire thread samples, which is flat. Looking back I wouldn't bother with it. The wire coiling round the 1.5" pipe prevents the whole alternator from falling off when I lower it. At the juncture with the 3' pipe the inner hole was made too small and after several futile attempts to push through normal cables I had to change them to the same dual magnetic wires I wound the coils with so they are small enough to pass through. Plenty of taping as you can see to protect them against the inner surface of the pipe hole.
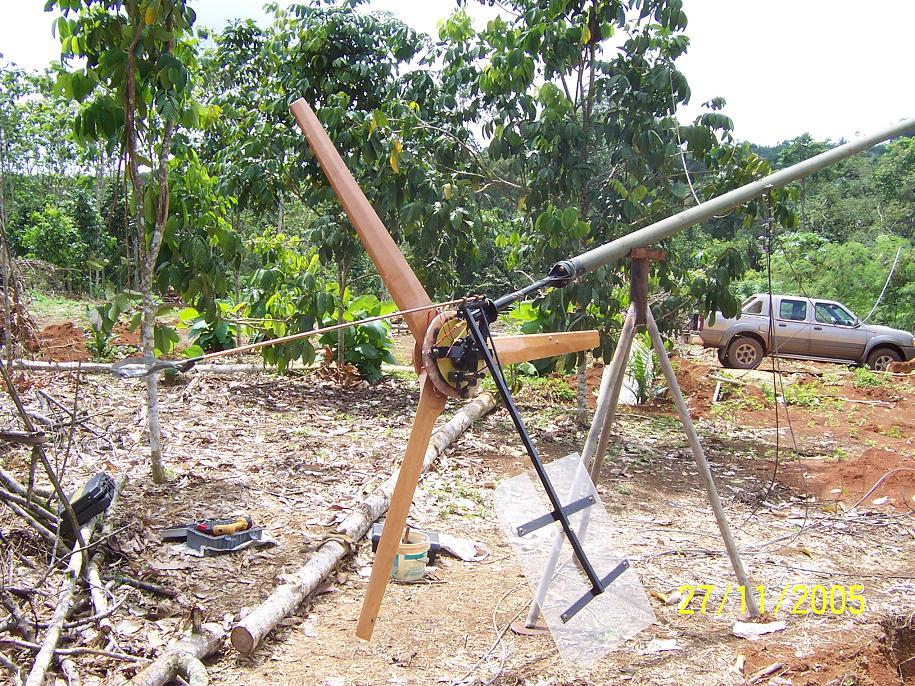
My Tail is plastic which should be more durable in tropical wet climate. Also note the lightning rod.
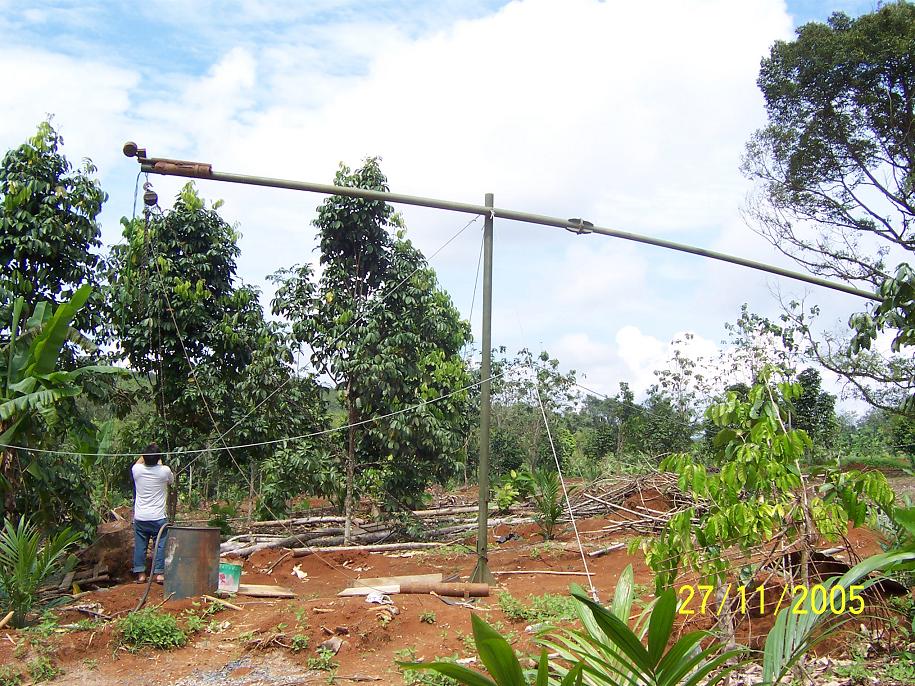
That's Tan Boon Hwa, my carpenter friend who made my blades for me. He is working the chain block to raise the wind generator. My version of tilt up tower with the main support provided by the center 4" thick pipe.
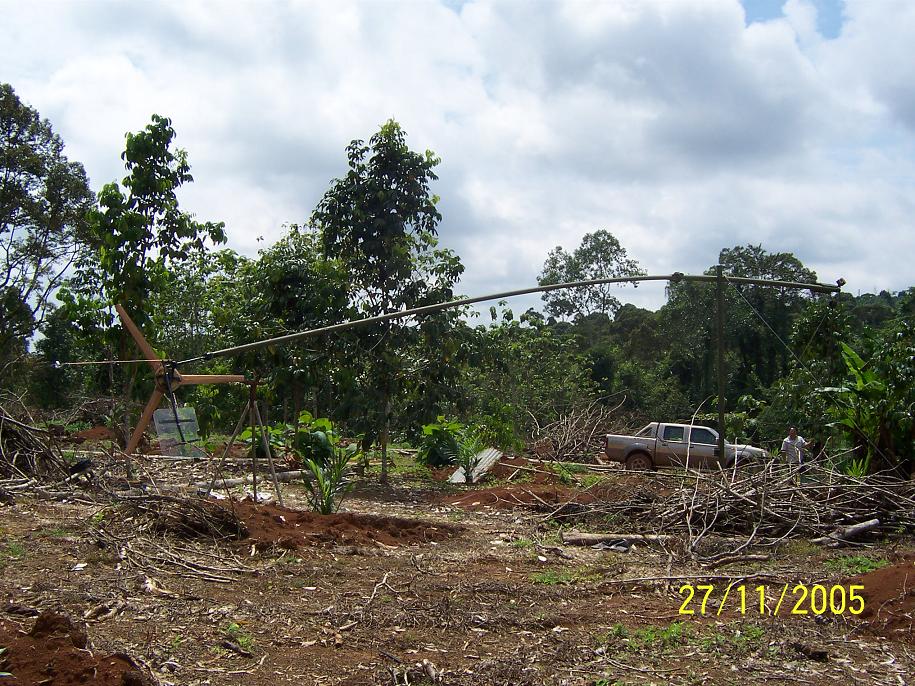
The slight bend on the upper limb is not the result of the weight of the windgen. When the tower was installed the lower limb was over weighted with 200+ kg of counter weight and we just could not pull the top down. This bend was inflicted when 4 of us pulled too hard. Finally the backhoe drain digger had to raise the lower end to bring it down. Also we cut off 100 kg counterweight.
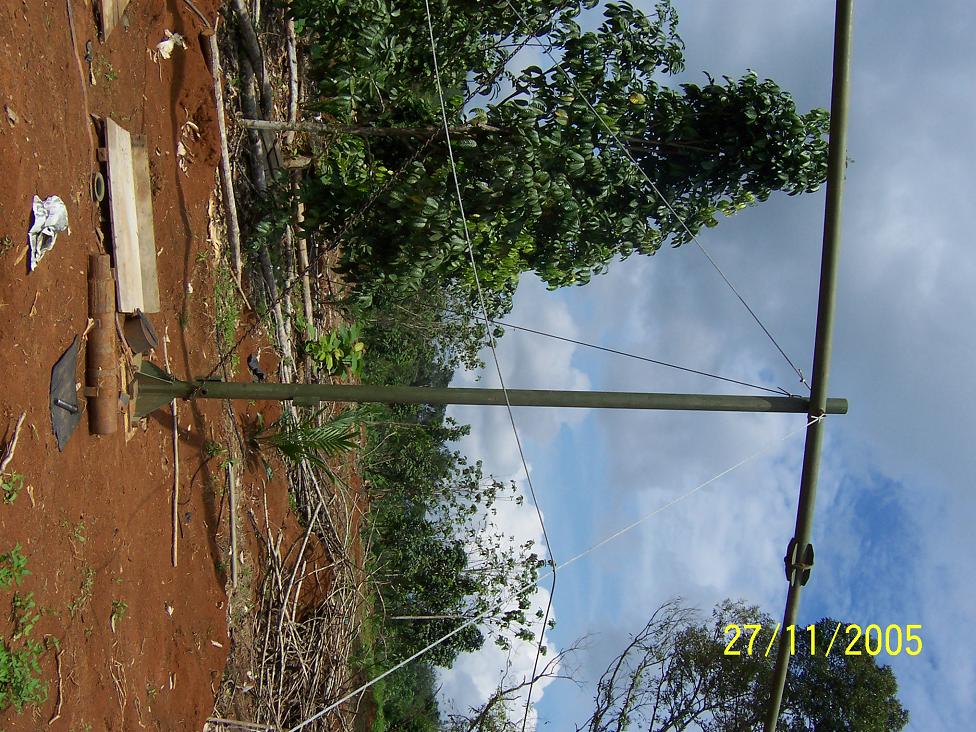
Another view of the tower. So sorry guys, I just could not get my computer to turn the photo right side up.
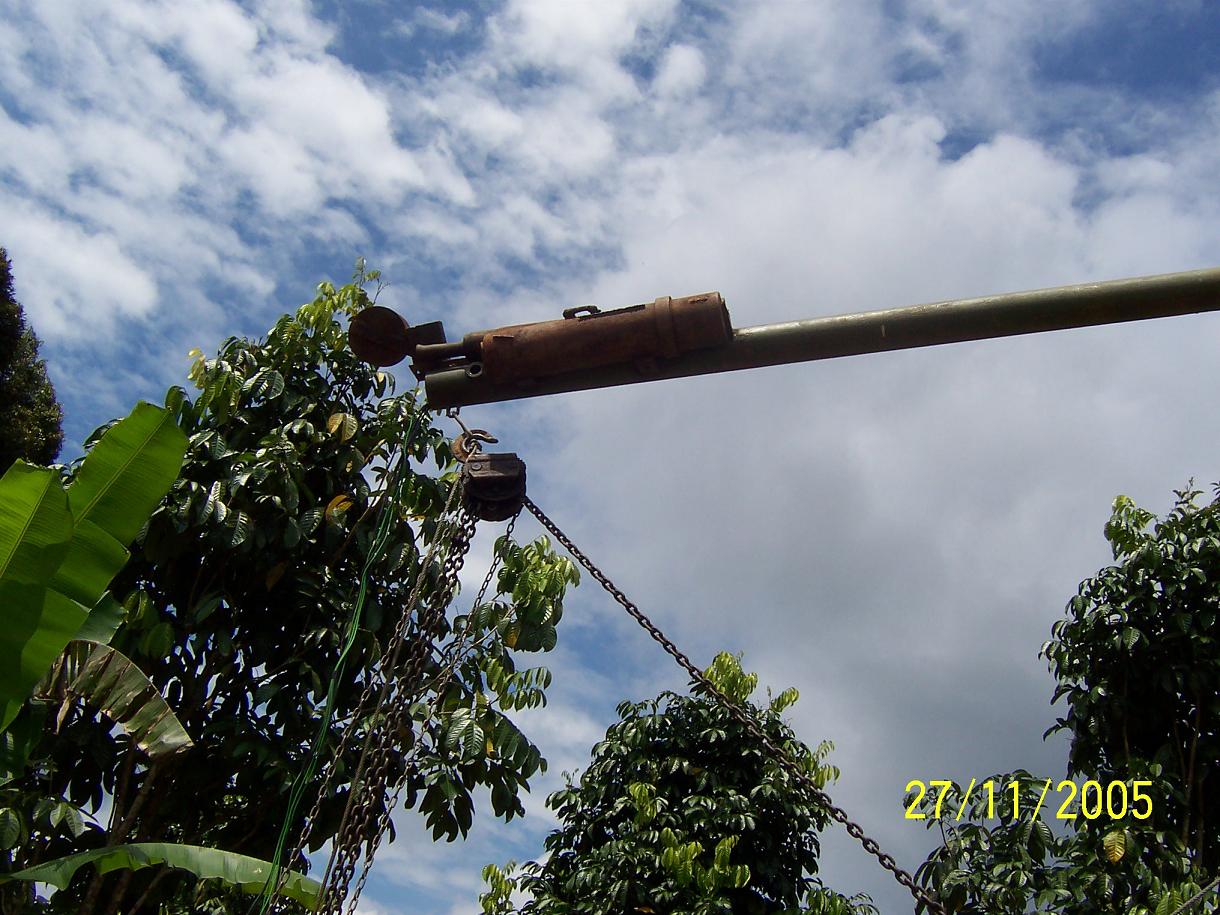
A closer look of the chain block and the counter weight at the lower end to reduce the force required to raise the tower.
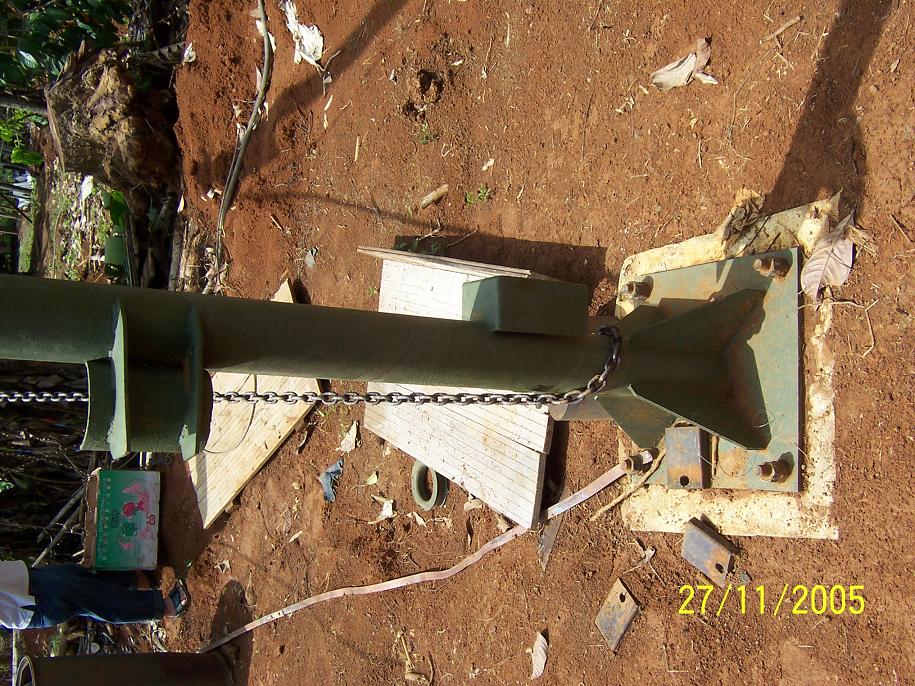
The footing on a concrete base 2' by 2' and 4'deep. Notice the bracket on the left of the photo, which stops the tower at the vertical position. A 1.5" diameter pin at the level of the box just above the footing locks down the tower when erect. The pin threads both 4" pipes and at the box end there is a hole in the pin to insert a lock to lock the tower. The box is to protect the lock from being cut or forced open
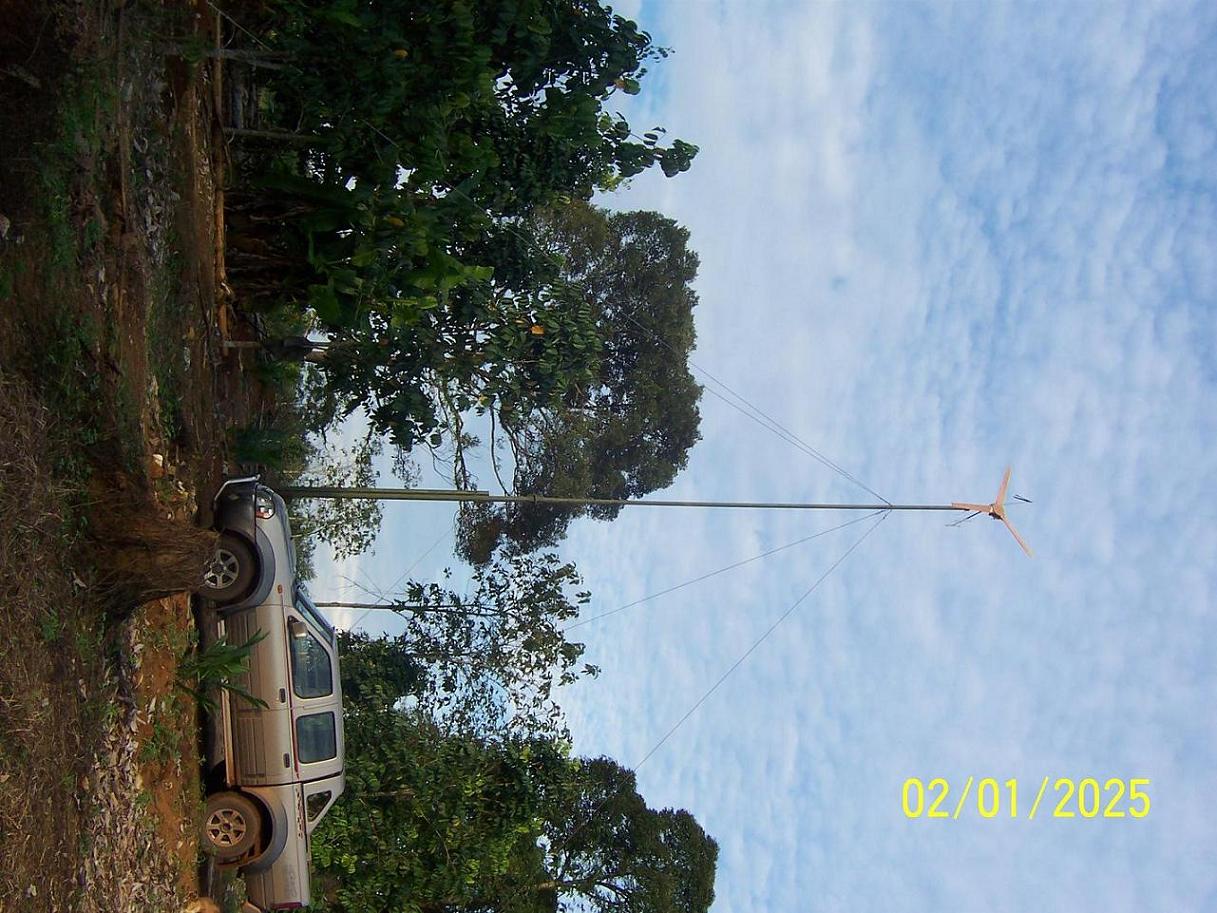
Here's the full 53 feet height of tower with all the 3/8" guy wires on.
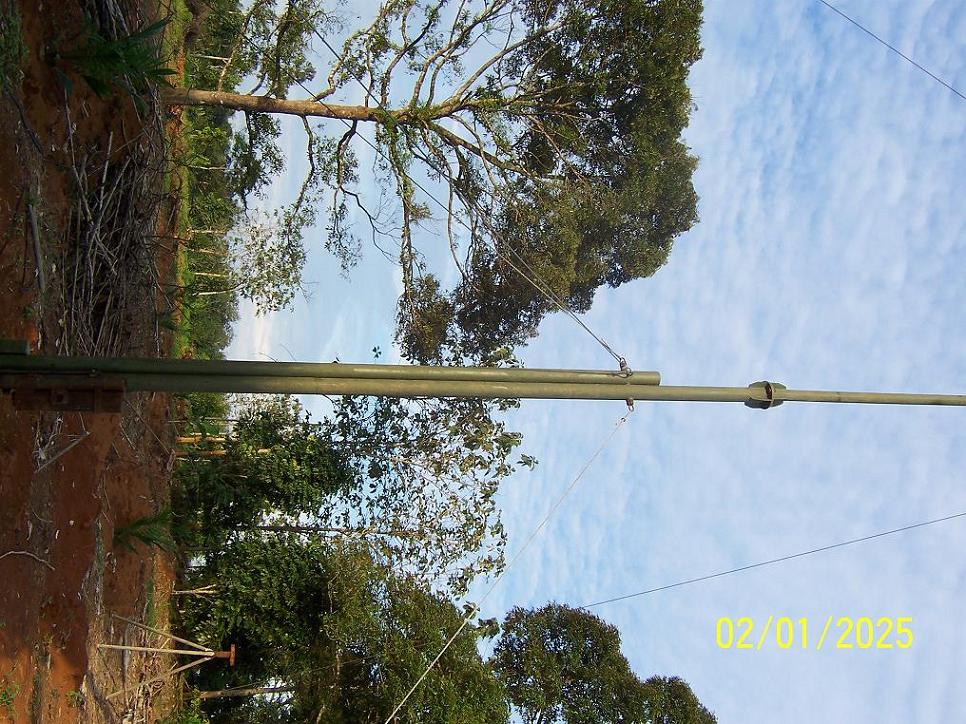
Side view of my tower. The costs of second hand 4 inch and 3 inch pipes cost only about 120/= US dollar. They were made for gas pipes and real solid and heavy.
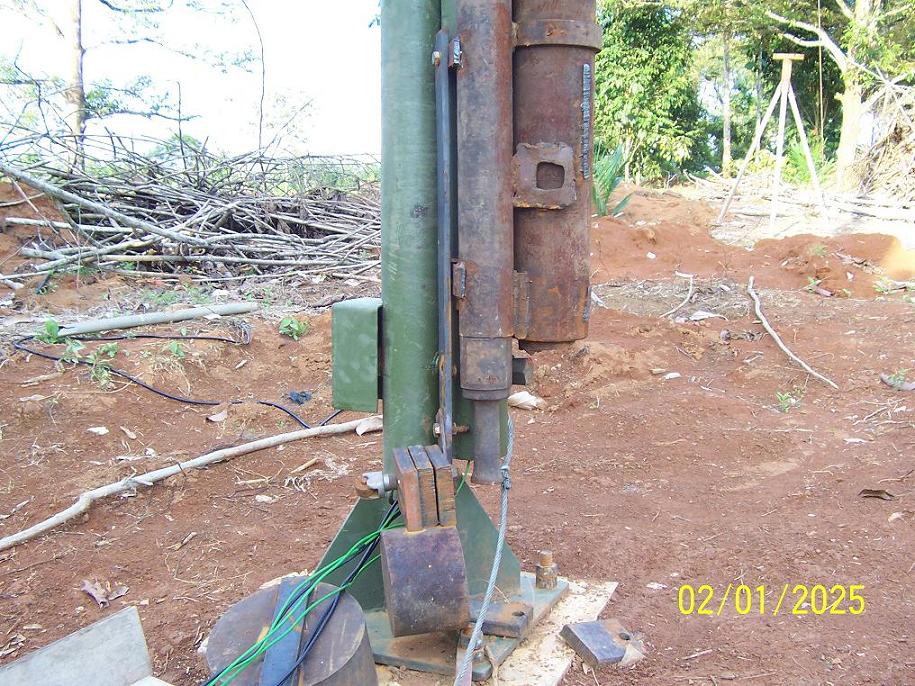
Counter weights with scrap iron. Note the round pin at the level of the metal box locking the tower down.
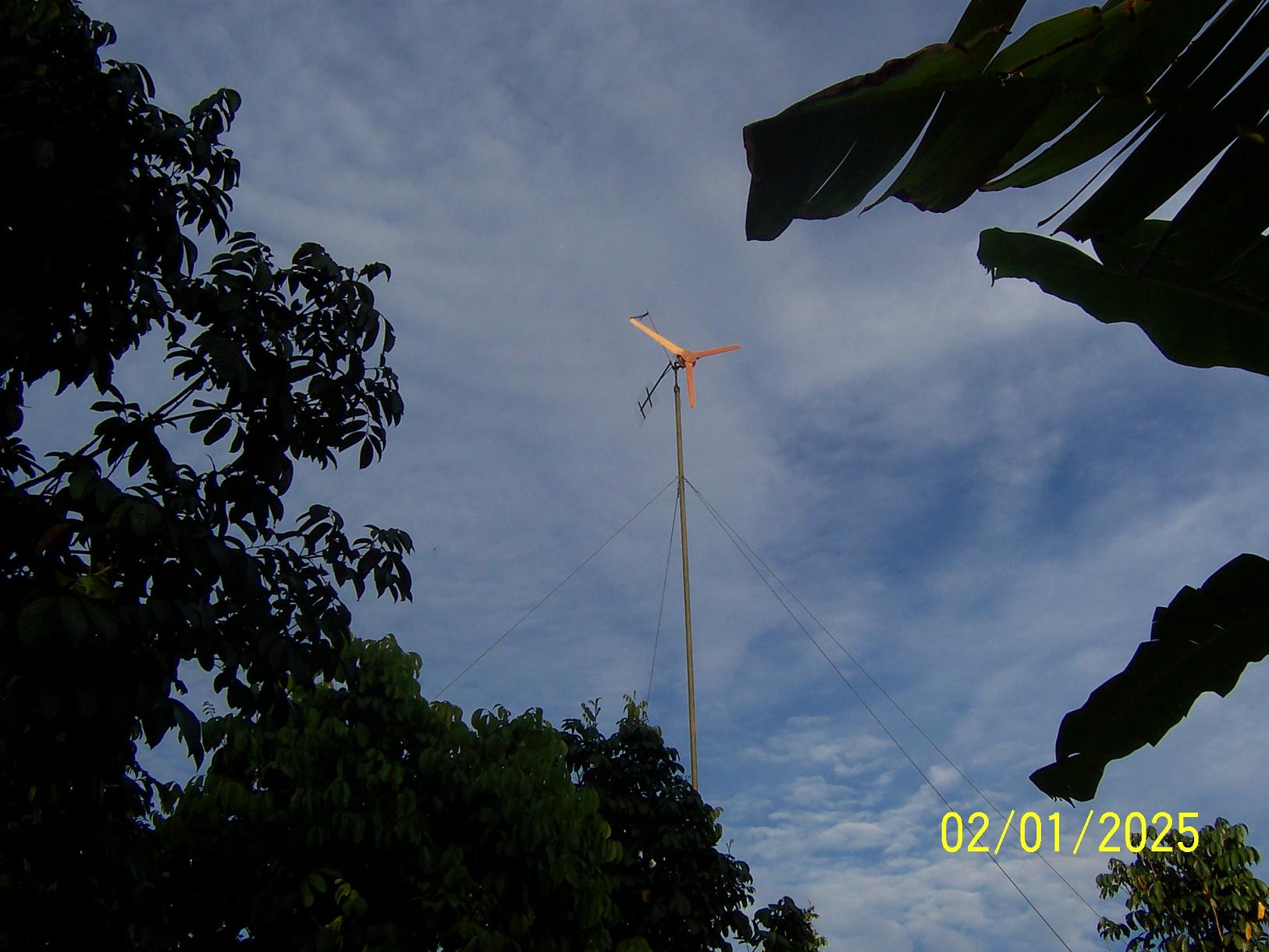
There it stands proudly in the sky and spinning quite fast but still not fast enough to show blurring of the blade tips. This may be the only wind generator raised in Malaysia.
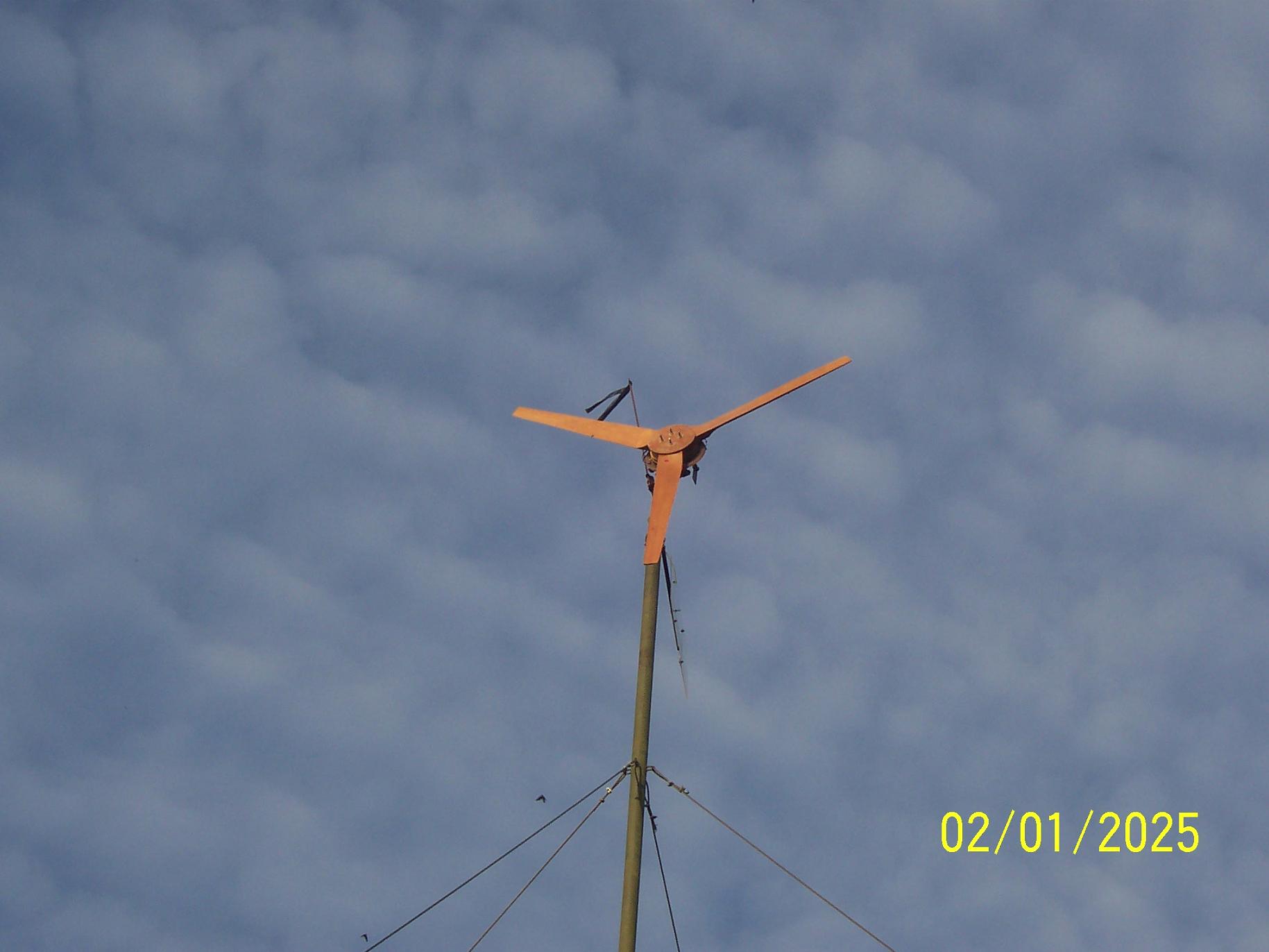
Here it is fast enough to be charging, just a few amps. Wind is at best sporadic and often changing directions with gusts of stronger winds when the amps go up then soon drops back. I must be one of the slowest to finish a simple wind generator system. Started in early June 2005 and finally raise the system in end November 2005. Then it took a good 3 months till today when I am getting something workable from it. Still it has been a very enjoyable and gratifying experience plus learning curve. When I read how Dan B and his friends finish their projects in a day or two I really feel real incompetent. My sincere thanks to Dan B for valuable guidance all the way, Flux for all my questions (off times stupid ones too) answered so thoroughly along the way, Ungrounded Lightning Rod for teaching me about static & dynamic balance of the blades and Nando for the test check list on the shunt regulator. Finally my thanks to all otherpower discussion board participants from whom I gleaned much information whether asking or answering.
SeanChan.