I've come up with these numbers and "conclusions" based on the math I've gleamed from what I've read... but this is my first mill and I have zero experience with what the numbers really mean. Any help from folks that know what's going on (unlike me!) would greatly appreciated. Thank you, - Ed.
I'd like to get 250 watts in a 12.5 mph wind. Betz limit at 12.5 mph is about 5.8 watts per square foot. It's suggested that a "good" turbine will get about 60% of that; I hope to build a good turbine! 250 watts / 5.8 / .6 / pi and take the square root of that for the radius of the needed blade equals 4.8 feet radius... so that's where I got the idea of a 10 foot mill.
Advice here was to build the alternator first, though, before carving blades so I did. Here's a picture of my alternator -
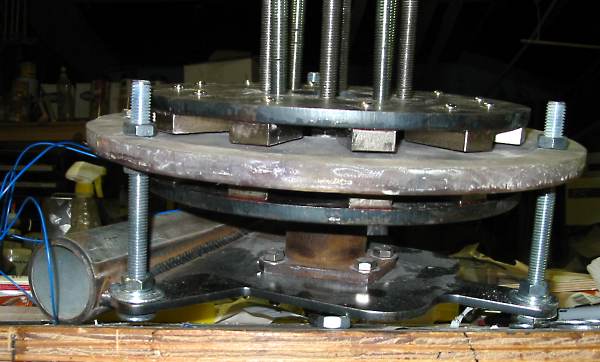
It has 24 1x2x.5 N42 neo's on 3/8" thick steel rotors.
The nine stator windings are #15, two in hand, 48 turns and 1/2 inch thick. The casting is 9/16" thick. The winding resistance is .3 ohms (based on 35' of wire). I originally did my test coil with a 7/8" air gap but the stator came out nice and flat so I did "final" testing with both a 3/4" air gap and a 7/8" air gap.
(Note: there's fewer turns than traditional in the coils for a 24 volt system because I want a better match and less heat at higher wind speeds; I'll use a boost converter to get charging current out of the coils at lower wind speeds.)
Testing the alternator with a 3-phase rectifier with 300 ohm resistor on the output, I calculate 25 volts out at
210 rpm with a 3/4" air gap, and
245 rpm with a 7/8" air gap.
Assuming a 10' blade with a TSR of 7, cut-in mph for 25 volts are
10.5 mph with a 3/4" air gap, and
12.3 mph with a 7/8" air gap.
How much power?
Using the method for calculation power described by flux, the mill with a 3/4" gap would produce
855w @ 17 mph, and
1262w @ 20 mph
Total output from the alternator would be 1262w to the battery plus 1180w in heat in the stator for a total of 2442 watts. Besides being concerned that the stator would melt in 20+ winds, I don't think that the mill would get there... power out for a "good" turbine (.6 x Benz limit) at 20 mph is 14 watts/sq-ft. 2442/14 = 175 sq-ft which would be a 15 foot mill!
The mill with a 7/8" gap would produce
- watts at 17 mph
- watts at 20 mph
Total output from the alternator would be 866w to the battery plus 564w in heat in the stator for a total of 1430 watts. 1430/14 = 102 sq-ft which would be a 11.5 foot mill...
On the other hand, the 530 watts + 220 watts of heat at 17 mph = 750 watts divided by 8.59 watts per sq-ft for a "good" turbine in 17 mph wind yields a requirement for a 10.5" diameter blade... seems like it would just be starting to stall.
--%--
I'd like the mill to furl somewhere shortly after 20 mph winds.
I don't know whether my notion of stalling based on "how big a blade is needed for the power output" is really how stall is estimated or whether I should be stalling a little bit (but not a lot) or not before furling.
My gut feel is that the gap should be at least 7/8" but I don't know if I should make it a little bit bigger...
Thanks a lot!
- Ed.