I was able to set up the additional test. The first test were done at just a couple amps so no thermal testing could be done.
It was evedent from the first test higher rpm and a lower battery voltage load would be requiered for higher amperage and higher heat testing.
The first test with the smaller GE motor and the large yellow 12 volt battery was conducted at my retail store/shop.
Todays test was done in my home shop. It was cold but i got it done.
I used 12 each 6 volt golf cart batteries wired in perelell. I figured this should provide a fairly solid load. I set the PMA up with a belt drive from a 2 HP 180 volt DC motor.
I have a 5KW variac here also and a 200 volt power supply. So 0 to 200 volts dc to vary the rpm.
I used 4 digital meters. I measured voltage and amperage going into the drive motor and voltage and amperage going into the 6 volt battery bank from the pma.
I also used an infered remote thermomiter and an infered romote digital tachometer.
Since the alt has been tested at very low amperage I omited these #s here and will report #s at 12 amps, 15 amps and 20 amps.
I tested the star stator first. Here are the #s.
12 amps at 1509 rpm, temp 49%, drive motor at 360 watts.
15 amps at 1722 rpm, temp 90%, drive motor at 500 watts.
20 amps at 2165 rpm, temp 100%, drive motor at 832 watts during this test the armature started to get real hot and I could start to small hot reson.
Next "Jerry Rigged" #s.
12 amps at 1432 rpm, temp 42%, drive motor at 322 watts.
15 amps at 1563 rpm, temp 47%, drive motor at 408 watts.
20 amps at 1802 rpm, temp 53%, drive motor at 598 watts.
I drove this stator up to 25 amps then it began to get hot after a while. Star got real hot real fast at 20 amps.
Here are several things I have determined from these test.
1. star requiers higher rpm.
2. star produces less power at the same rpm.
3. star requires more drive power.
4. star produces more heat in the coils while at the same time requireing more drive power and produceing less.
I've noticed very simular results in last years GM alt test and the 3 phase motor conversion.
It has been sugjested that wave form would effect these test results. I don't think a GM alt, a 3 phase motor conversion and a dual rotor disc alt would have the same wave form and yet they had very simular test results.
I do have more testing to do on a few more disc alts. I think the fun will be with the larger high amperage machines.
Here are a few pictures of todays test set up.

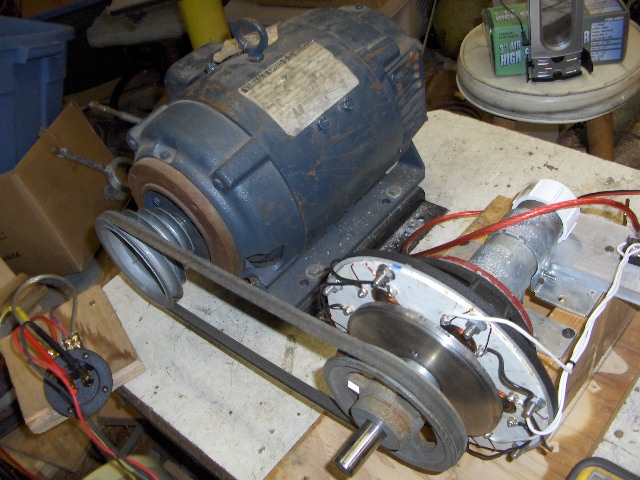
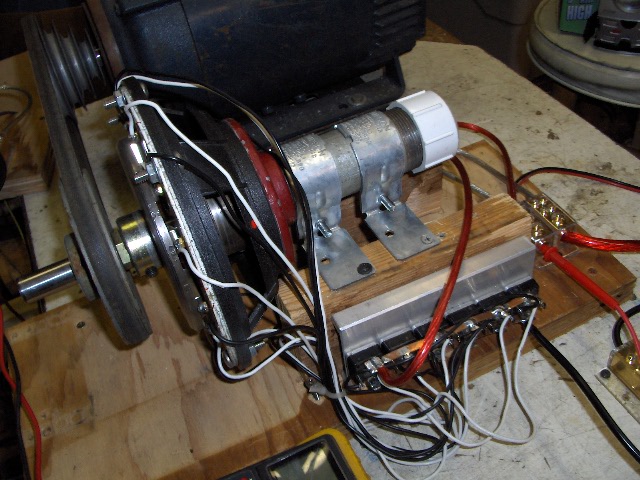
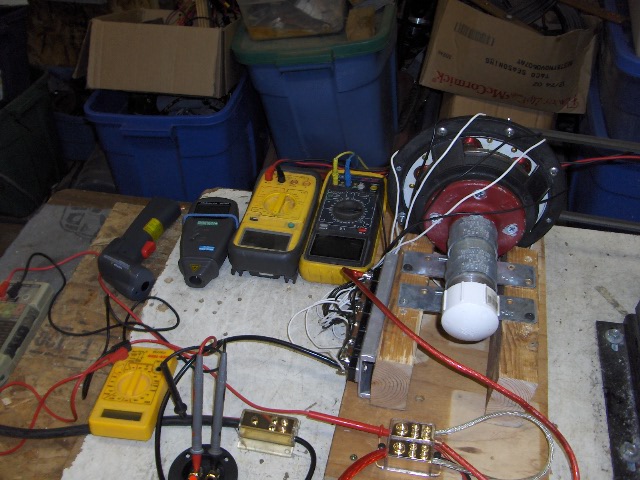
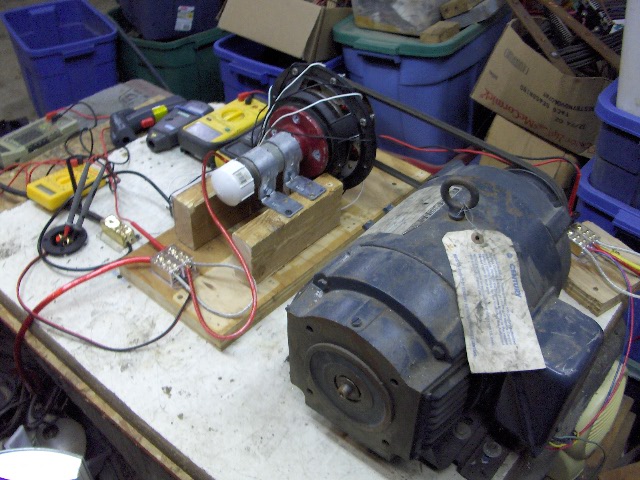

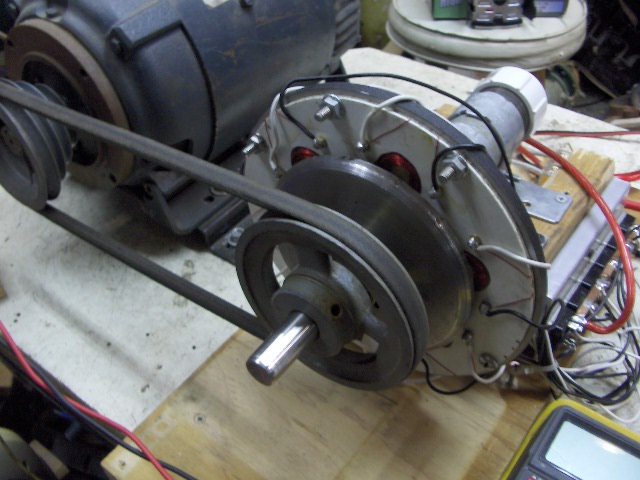
I have a few more dual rotor alts started but it will be some time befor there ready for testing.
JK TAS Jerry