I'm building an alternator for my 10' prop, thought I'd post some pictures of the making. Comments and better ideas are still welcome if you see something odd

It's going to be a 12 volt 5 phase unit, with each coil connected in star and the 10 ends going to rectifiers. I think i can better avoid circulating currents by not connecting the coils in parallel, but instead bringing all the leads to the rectifiers.
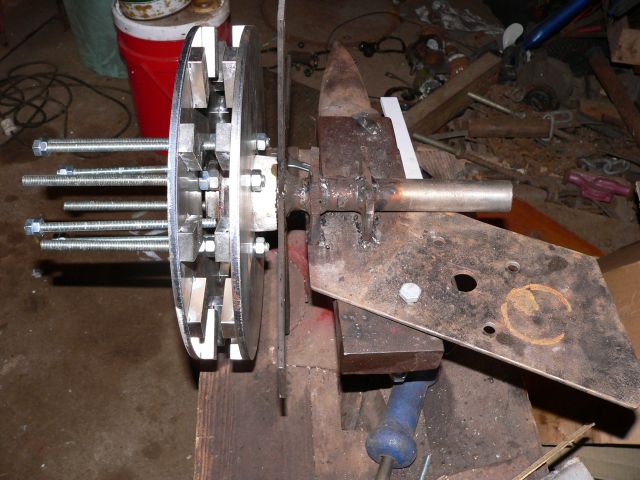
here's a shot of the current state of the alternator. I assembled the magnet rotors to test what number of turns I'd need for the right cut-in speed. The hub(bearing) is from a Saab 90 car.. it should be more than able to handle the loads experienced here. I'm going to use the other rear bearing for yaw bearing.
I still need to weld the tail hinge and additional bracing to the frame before it's ready for paint.
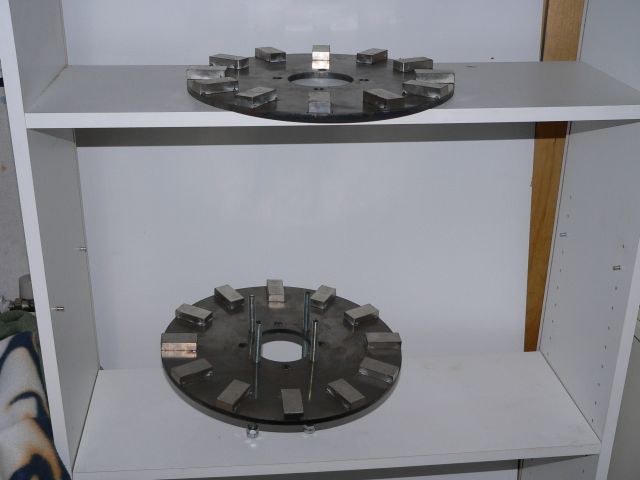
The magnet rotors. Magnets are just tacked in place with super glue. I needed to jack the first 6 cm's with the jacking screws, after that i was able to pull them apart with my hands. I'm planning not to cast them in resin, but glue them in place with epoxy, and add a stainless steel band around the magnets for extra insurance.
The magnets are the common 2"*1"*0.5" sized, ordered from the host site.
The discs were laser cut to ease the progress. Well worth the money, I think.
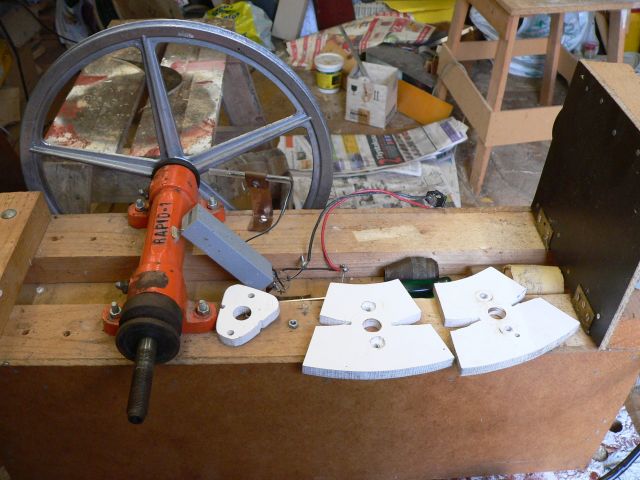
A shot from my coil winder. There is also a dc motor attached(bottom shown in the right edge of the picture), but i'm not using it this time. The coil formers are made from a 10mm thick "COP plast", a foamed pvc board with hard "films" on top and bottom. There is also a reed relay and a counter to ease counting the turns on the coil.
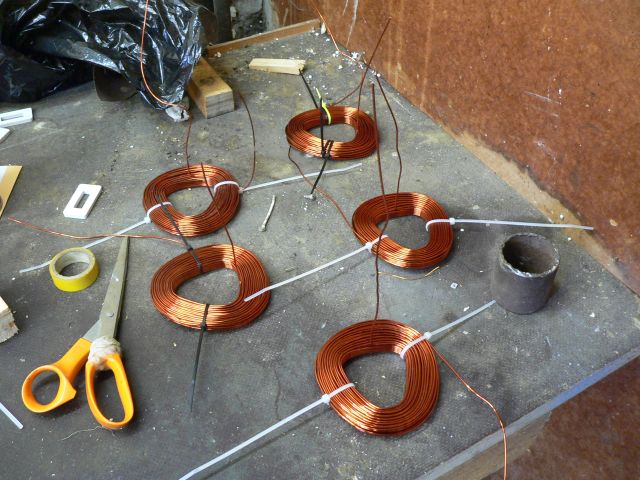
I managed to make 5 coils before i ran out of magnet wire. They're 1.4mm thick wire(about awg 15), with 95 turns on each.
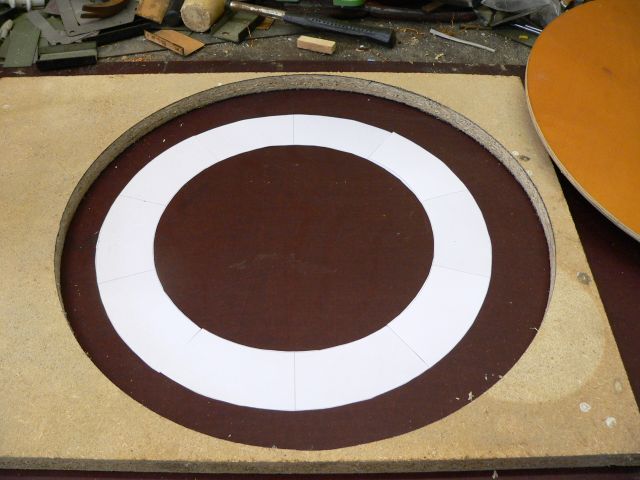
Stator mould. Not showing the picture are the top lid and center island. I'm planning to use regular polyester resin with fiberglass mat reinforcings. I'm aiming for total stator thickness around 11mm, which would allow a nice tight airgap for earlier cut'in. The average winds around here are rather calm, so i think earlier cut in is the way to go. I made the mould with a hand router.
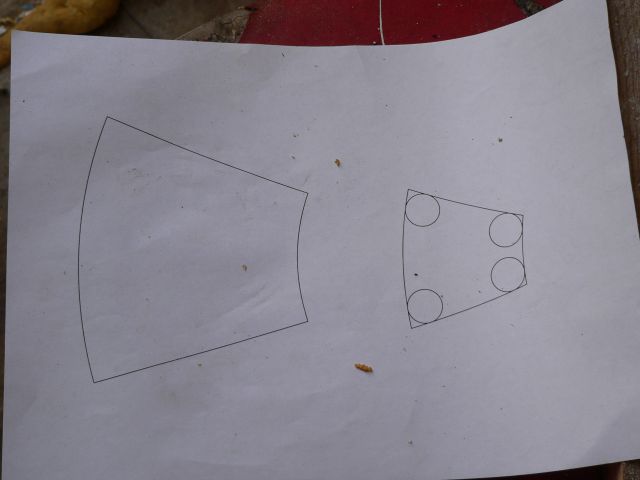
When i need a specially shaped part, I like to first draw them with cad, print them, and use it as a guide to cut the part with a band saw. It seems to work rather accurately, kinda like the poor man's CNC machine.
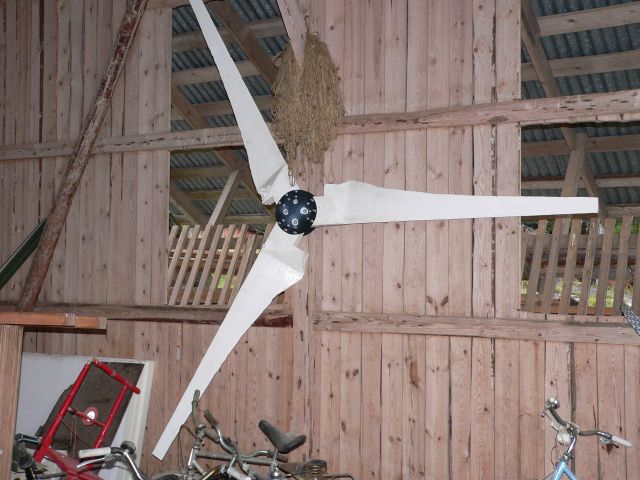
The 10' prop that was carved earlier, it's proven to be good, but was a bad match for my first attemt at making an alternator.
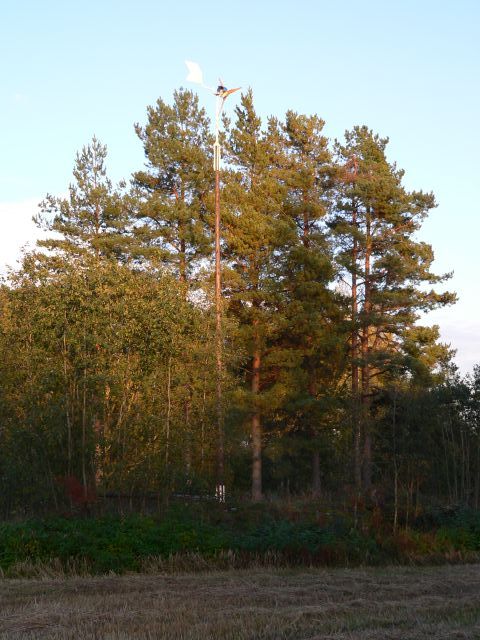
After the 10 footer is complete, it's going to replace the 5' machine, completed earlier this summer. It works ok, but is not producing nearly enough power in the low winds we have here, especially in summer time.
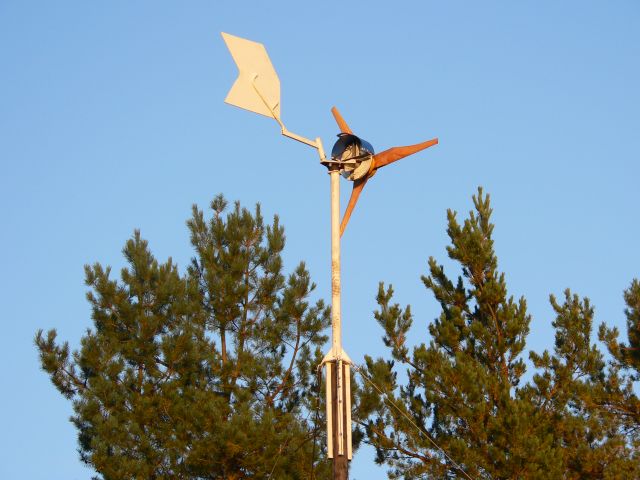
Closeup of the 5 footer. Those trees are going to be cut down, after that there should be more than enough free space in all directions.