One of the things I learned was----the typical yaw bearing
(pipe over pipe) without something to spread the weight and the
wear is not a good idea. I've seen other postings here that confirm
that. It doesn't take long for the end of the pipe to wear through
the flat plate that's supporting the weight of the generator head.
My solution is a 4 bolt flange bearing. Add a couple of pieces of
angle onto the bottom of the yaw so that the bearing has a flat
surface to bolt to.
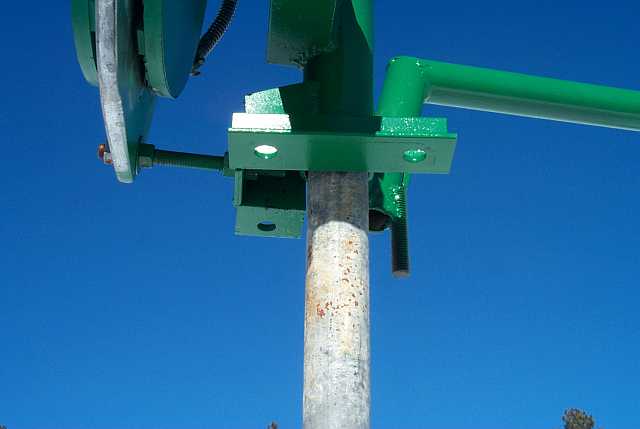
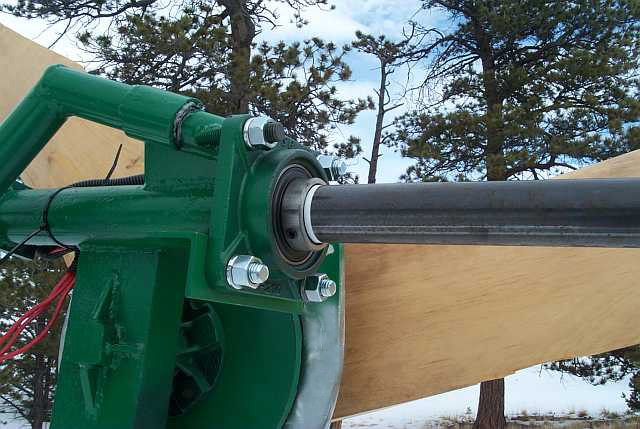
Set the bearing so that there is a clearance of 1/4 to 1/2 inch
(6 to 12 mm) between the end of the pipe and the flat plate stopper.
Paint a white line around the tower stub at the point where the bottom
edge of the bearing will sit. The white line will tell you if the
bearing has slipped and the pipe is once again rubbing on the flat
plate. It's visible from the ground, so you will know without having
to lower the tower and check.
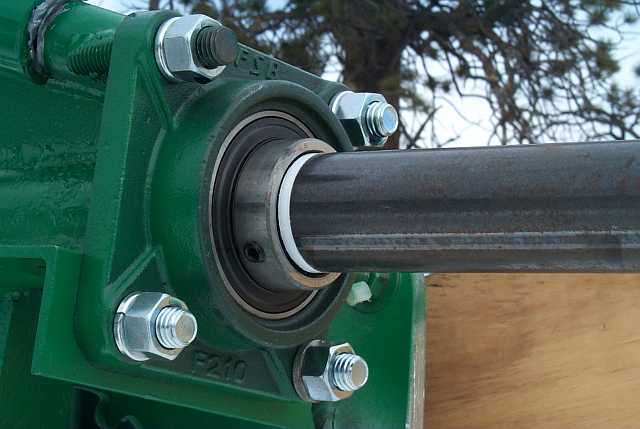
The next thing I learned was to install a grease fitting on the side
of the yaw bearing. I tried greasing the tower stub and then slipping
the yaw over it.
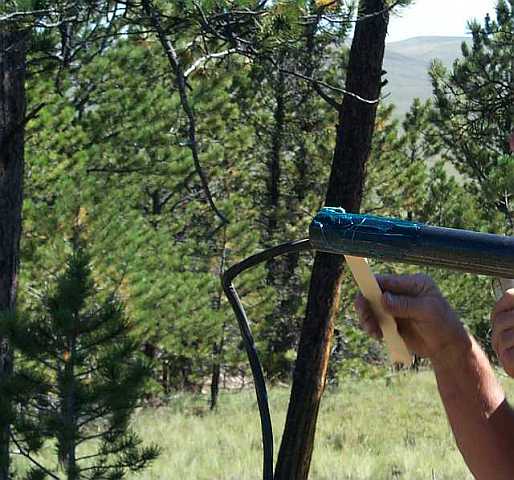
No matter how I tried, I always ended up scraping half the grease off
with the end of the stub. The simple solution is to install a grease
fitting (or 2) during the building of the yaw. Put the yaw on the stub
and pump the grease gun until your arms hurt. You don't end up looking
like a greased pig! I don't have a picture of the grease fitting.
The lesson that really hurt was the one that cost me a set of blades.
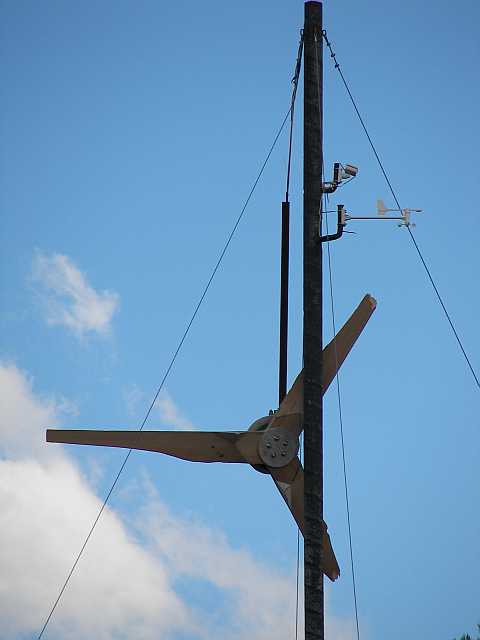
The tower stub needs reinforcing where it meets the tower. My tower
is 4 inch black pipe. The stub is 1 1/2 inch black pipe. It never
entered my little brain that it would need bracing. The end
result can be seen in these pictures.
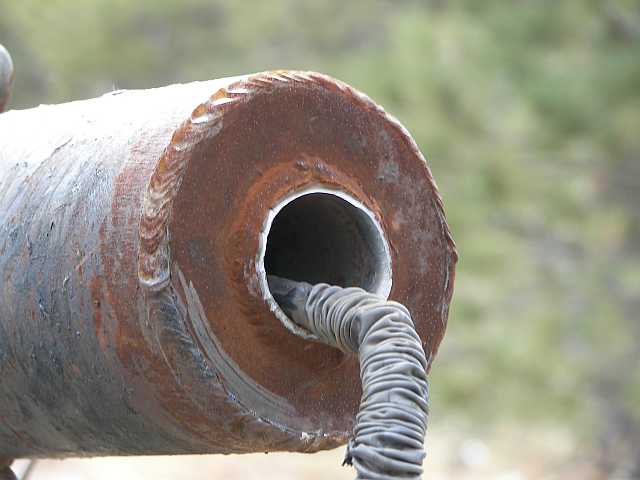
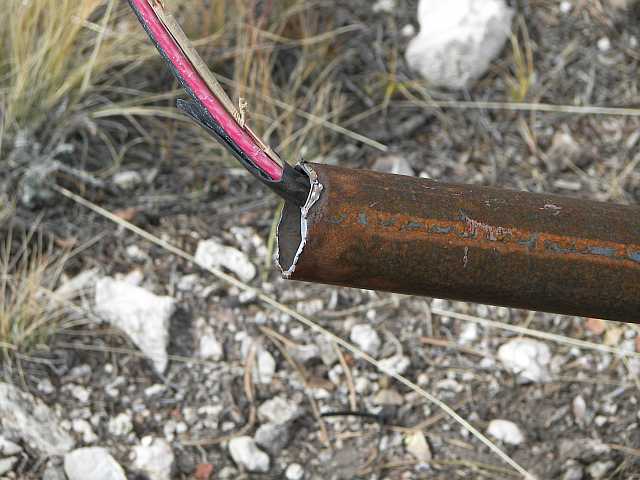
The stub was constructed of 2 large washers and the 1 1/2 inch pipe.
One washer, welded to the bottom end of the stub, slid into the 4
inch pipe. The other washer, about 18 inches up the stub from the
first was welded to both the stub and the top of the 4 inch pipe.
I just knew that was a very secure joint!!! Wrong!!!!!!
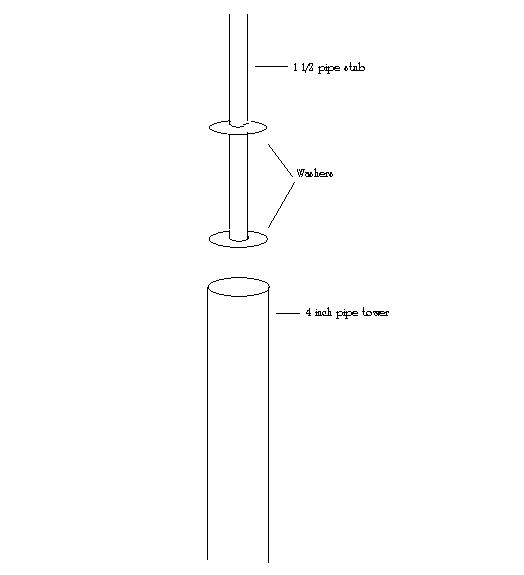
Here is a picture of the broken stub after it was cut from the
top of the tower.
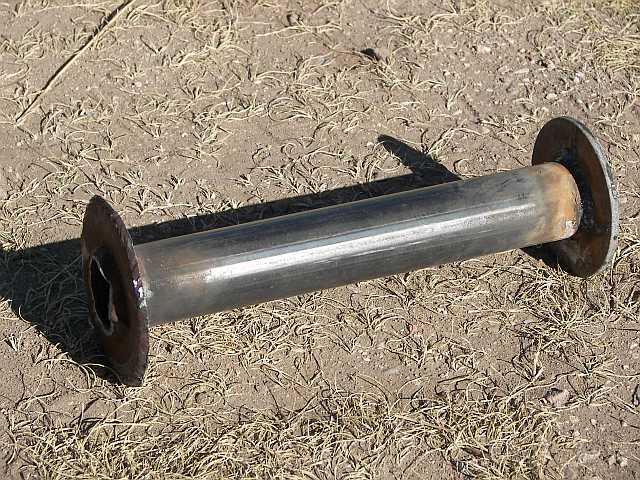
I now know that you either need some triangle shaped braces or
another piece of pipe inside of the tower stub.
At the time mine crashed, I didn't have any 1/2 inch thick plate
to make braces, so I opted for putting a piece of 1 1/4 inch pipe
inside the 1 1/2 inch tower stub. Those 2 pieces are welded together
on each end. Then the washers are slid over the 1 1/2 inch pipe and
welded into place. Then the whole assembly is slipped into the 4 inch
tower and welded.
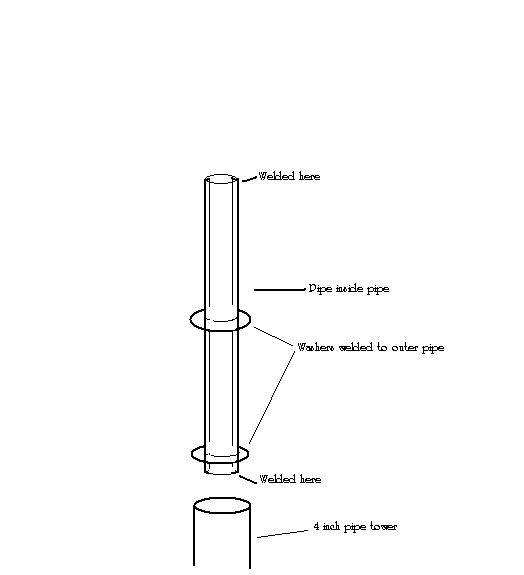
That way if the 1 1/2 inch stub cracks and breaks where it
meets the tower, I will have a little help from the inside pipe. It may bend, which is
my warning that something is wrong. That way I can lower the tower and fix it .
Hopefully without destroying my blades again.
I hope these things will inspire others to show the lessons that
they have learned.
Maybe we should have a section titled "Things I Learned the Hard Way!!
Ralph