Hi All
Pics here are of panels I bought earlier this year. They were described as "new but damaged" although mounting holes in frames on some had been used. I got 8 panels of 175W, 185W or 200W panels and all had broken glass, mainly crazed but some impact damage.

I purchased them from a guy in Germany who had a stack of them in his lock up (possibly from a factory auction???). He spoke little English but was happy to let me test them before purchase and he did not seem to know much about them. They gave good power and still do, although probably down a little on actual rating, due to crazing and the extra, non specialist glass. I don't know exact figures as I'm waiting on a regulator and meter to start using them properly but they bought a set of 2V forklift truck cells up to excited mode before I had to disconnect them.
I first looked into a plastic sheeting to get a seal over the crazy paving but got very mixed info from manufacturers on how long their products would last, from a UV point of view. Plastic was more expensive than the glass too and by the time I got round to the job, I had moved abroad to where no plastic is available. I fixed a plate of new 4mm glass over each panel. The first one I tried, I used no more nails type stuff to bond the glass to the ali frame (I had some free and it is reasonably flexible) and glazers cheap glass silicone sealant to seal around the outside. I laid panel down on flat surface and ran a bead of each around cleaned aluminium frame, before laying glass on top.
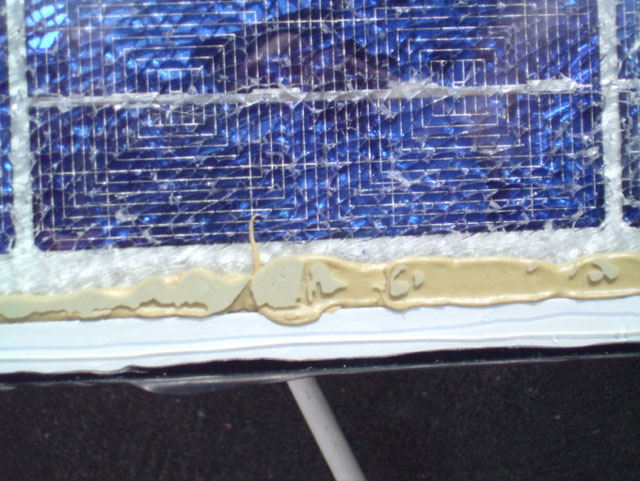
Pic shows No More Nails, silicon and then black adhesive beads
Glass did not touch all of bead without pressure and I did not want it to set with a tension in the joint. So once dry I put extra black car windscreen/windshield adhesive into gap around outer silicon bead. For the other panels I just used the windscreen adhesive and they have been fine. When just using windscreen adhesive method used was to lay panel on flat surface, put 2 small cork spacers on each edge and lay glass on. Then inject adhesive in gap and when partially set, take spacers out and fill spacer gaps so there is continuous bead around. The exact sealant used is Sikaflex 255-C Primerless Windscreen Adhesive. 2 to 2.5 panels per tube of silicon, with thick bead. Panels are about 1x1.25m in size.
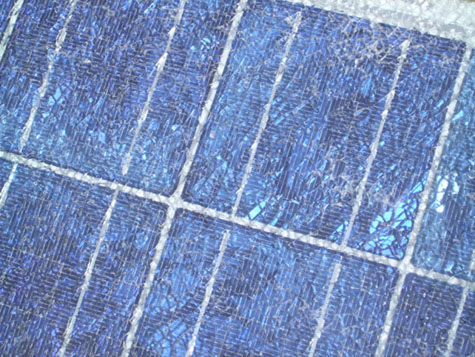
The panels have been outside in sun and rain (a lot of latter this summer) for about 10 weeks now and they are fine with no leaks or condensation. The bonding job was done inside the house but our local atmosphere is quite humid but no problems so far. I am still a little worried that there may be long term greenhouse effect (air heating inside, between panel and glass, not CO2 in the Earth's atmosphere, although that itself is still a bit of a nag!!) from the glass as there is a gap between it and the crazed original glass, of about 2 to 4 mm but so far so good. Two things to note are the glass makes the panels pretty heavy but less that 4mm would not be strong enough. Secondly is that the panel/glass set up does not have enough strength to allow you to pick up panel at a corner. Frame twists and glass will crack (been there, done that, got the T-shirt) so be careful and lift whole edge evenly to keep panel square at all times.
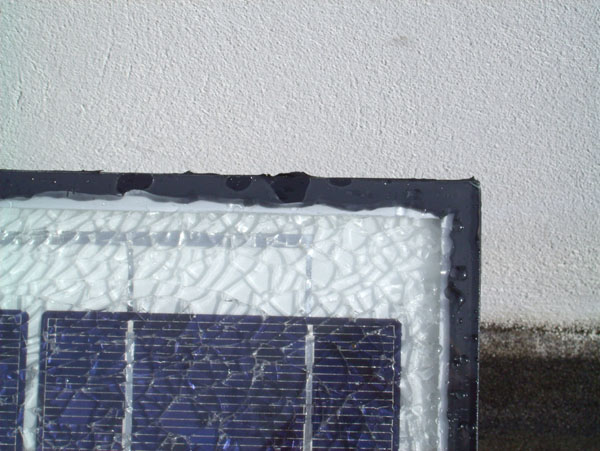
This shows nice wide bead of windscreen adhesive with good adhesion
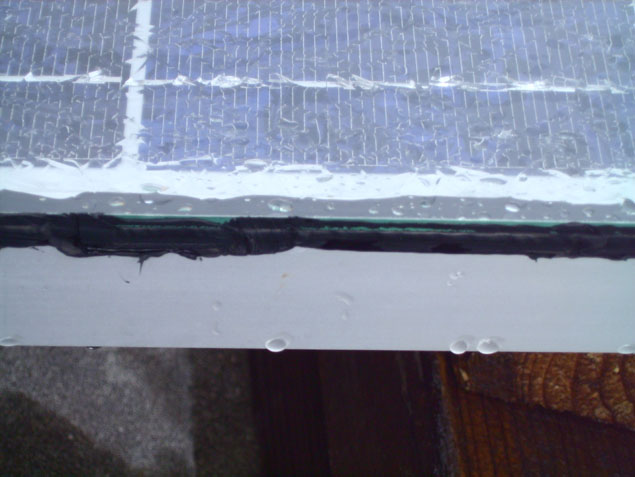
1330W of rated panels has so far cost about £1150 (1660EURO, 2150USD) to buy, transport, repair and fit so not too bad. It's my first RE project to reach fruition and will power an environmental education and research centre being built here in sunny Horta, Azores 38N, 28W. Greetings from the mid Atlantic.
Any thoughts always welcome.
Cheers
Chris