Mick-Mac Mick-mac, Wolf,
Brian,
You have done a fine job with your postings... Its really no suprise that TomW has given you'th the card'blan'chif...
Personaly, if your not the (chief)machinest and your wife is, then well, you have done quite well for your-self.
I talk to my own wife, about this stuff, and I get a bunch of deer-in-the-headlights(look), if you know what I mean.
I applaud you efforts...
To me, its about as good as an episode of 'how its made' on 'discovory channel'(soon to be 'green planet', by the way).
However,
Wolf makes a good point. You are about to enter a 'zone' with winding coils that your most certianly going to halve-too go back and forth a little-bit.
After-all you stated your about to build a coil winder. Now look, Flux is your best bet in getting info about how to wind your coils. What you seid last about going into a 'test coil winding phase' confirms all of our most worst night-mares.
You do have 24magnets with alternating pole bias within 2 planes with the dual rotor configuration, this makes us feel better. So each 12 magnet rotor will face an N-S within the indexed attraction for each rotor facing proximity.
It is unlikely, but possible, but unlikely that you have figured all this out for yourself, but again its possible...
Now looky here DanB is a serious dude. Last I heard he was subing out to a water-jet guy.
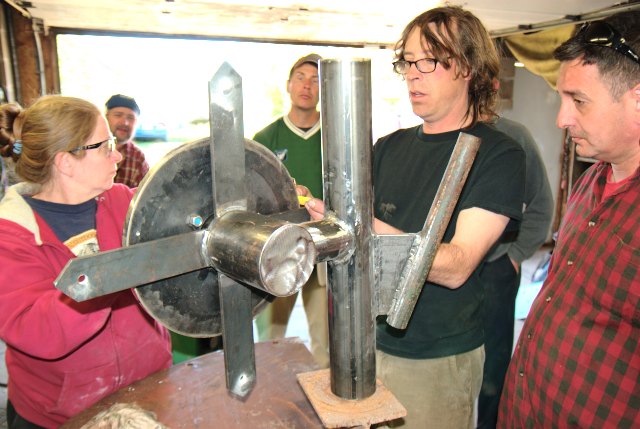
Im assuming you figured out the 80% html tag line thingy, Because your pic's are great.
One thing you have not mentioned, is your load use, and batt-bank capacity in watt-hours.
This will become extremily critical as you figure, cut in speed for your wind area, average winds, and how many days you need to charge your battery's from draw-down, like what you'd see from a load test of your intended batt-bank capacity. On the otherhand, im sure the critical info that you ask for will be tracked no matter where you post on the board, diary section for example. Also it has happened on rare occasion that Flux's diary posting's have made it to the front page. So what wolf is tring to say is not bad in anyway. But he was in a Russian cab, visiting his daugthers in Russia when that picture was taken. I think.
Now looky here, Dan has never called me Dead Wrong about any technical specs before (thank god) But he has stated this to me, about how I may percive other user's here. Just remember, alot of these guys are basically a PHD in this stuff, but you never really know who is who. AS ALWAYS
CAVE-EAT EMPTOR-
JW