I recently got a new CNC router. I've been trying to learn the machine and the associated software that goes with it. I hired a kid that is going to an engineering school to create some CAD drawings. It is based on the Dans design. It took a while to get it figured out how to make both sides of the blades. I think I have crossed that hurdle and can index it so that the back side is cut correctly as well. I made 3 24" blades and using scrap material, made a 4 foot wind mill that only spins in the wind. Those blades came out really good. The surface was really smooth as it came off the router so I didn't even sand them. With those blades under my belt, I decided to make some full size blades out of laminated cedar. They are going to be 6' long. Here are some pictures of the front side of the blade as they are being rough cut. I've made them so they will spin CCW.
The machine I am going to put them on is one that I helped build up at Dans. Its a 12 foot axial flux machine. I'm going to be data logging the power output. I'll get some good data using the Clark Y blade profile and hopefully be able to generate a power curve. Once I have sufficient data, I plan on making another set of blades with the NREL S822/S832 profile. Swap the blades out and see if they will increase the performance. It will be interesting if nothing else.
Mike
This is a rough cut with .1 inches overlap

This is the front side being cut with a finish cut
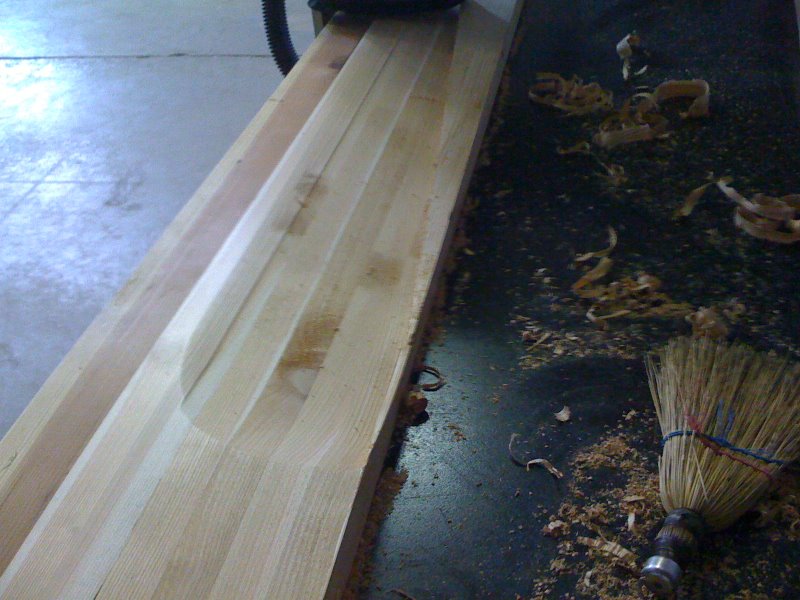
Here is the front side tip view with the finish cut on the right side and the rough cut on the left.
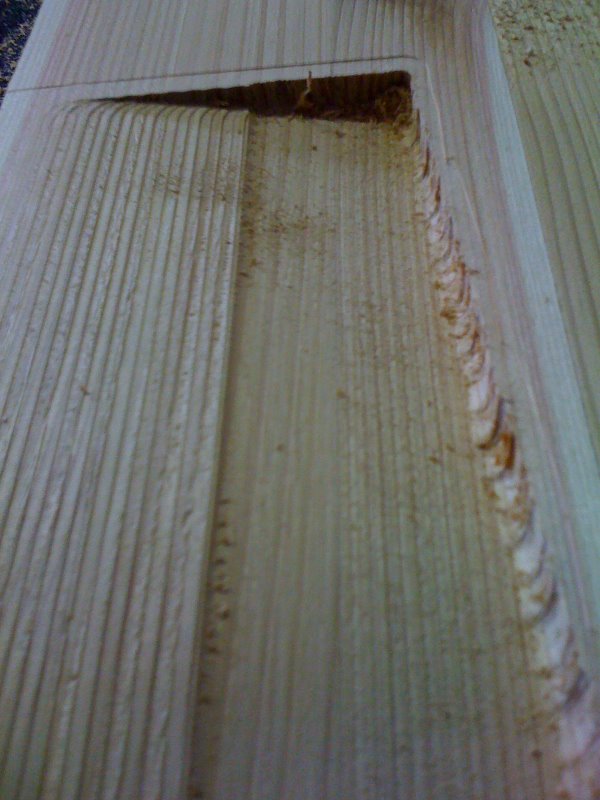
Another view of it just getting started.
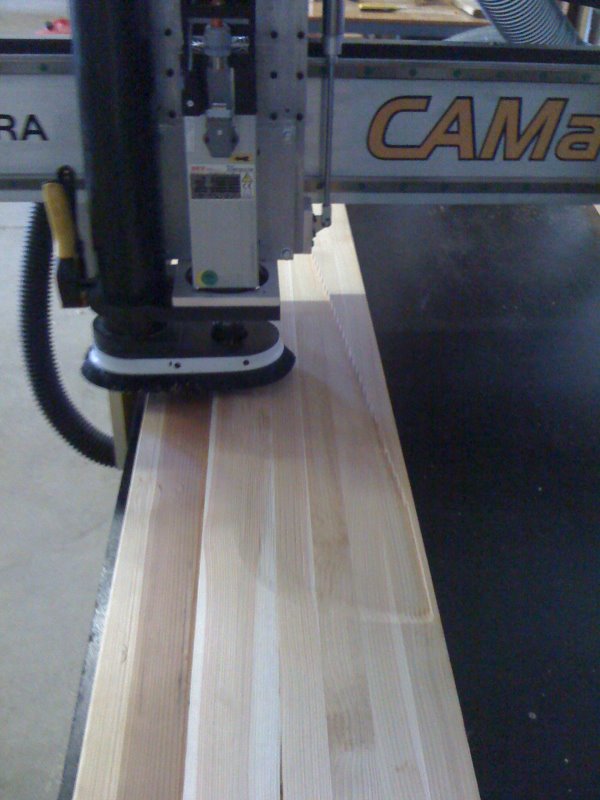