This is going to be my largest Alternator to date ,with 10.5 inch diameter rotors , actually a tad less , but not much.
And a substantial bearing to handle a nice set of wooden blades.
the Rotors are off a Honda Civic front brake disks, which just happened to be the perfect size for my mags.
The bearing is from the Ag supply store, i had to open the holes in the rotors up a bit , it wasn't an exact match on the bolt circle diameter

The thing about the rotors is they through the air outward when i spin it by hand, so i don't see the mags heating up that quickly , and the airflow should get sucked past the coils before exiting through the rotor.
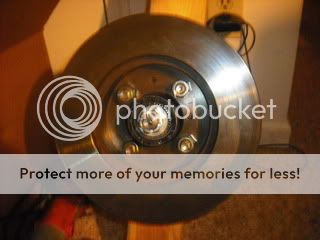
I am making a new coil winder also , with all the parts from Lowes .

The electrical department had the two key parts , 4" diameter electrical box covers , one to go next to the wire , and the other to support the perimeter ,with some black foam between. which i just Tapped to 3/8-16 thread.
The center of my coils is two nylon bushings , which when screwed down tight makes two fairly parallel plates , my calipers say they are just 0.004" from high to low reading around the
perimeter, 0.398" to 0.402". This is wider than i was planning on using 0.402/0.064" is six turns and change, maybe i'll just use one bushing , not sure at the moment.
Another thing about the rotors, they have 36 slots ,(between the two plates) so there is a slot every 10 degrees, and my mags need to go every 30 degrees ,so that part worked out nice ,
because i need to drill and tap for 1/4 inch machine screws to hold the mags in place . And its a good thing the webbing is not going to get in the way.
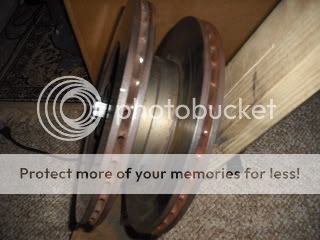
I need to paint them too, before i put the mags on, don't need them rusting the coating on the mags .
The plan was to use AWG 13 wire for this alternator ,but he didn't have any , so i got some real nice 14AWG wire .
I am expecting to get .75KW at times , out of this alternator , but i am secretly hoping for 1 KW , wind permitting of course.
I still have a LOT of welding to do , i have the bearing and the rotors on a 2by4 stand at the moment, and still need to replace the studs with threaded rod so i can turn the outer rotor towards the inner,
i did use an angle grinder to grind the hub down a bit so i could turn the inner rotor around, so the stator wasn't so far away from the stator mounts, when i get to that point.
anyway as soon as i get the threaded rod i will be able to adjust the gap between the rotors , then the test coil