Hi Mike,
I think you're going down the right path with the VAWT research. It's not the same kettle of fish as the HAWT units.
I hope there's a future for the verticals, and there might be for some applications.
It IS interesting to note that the power all happens at the front and at the back of the rotor plane.
I keep wondering if there's something that can be done to help widen out the power production band...
Here's a couple of graphs I copied from Dr. Gary Johnson's book, they're on the 17 meter Sandia Darrieus operating at 50 rpm.
First the definition of rotor angle:
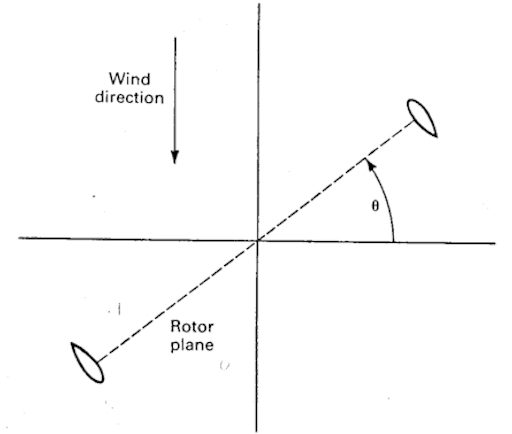
and the relative power output vs. rotor angle:
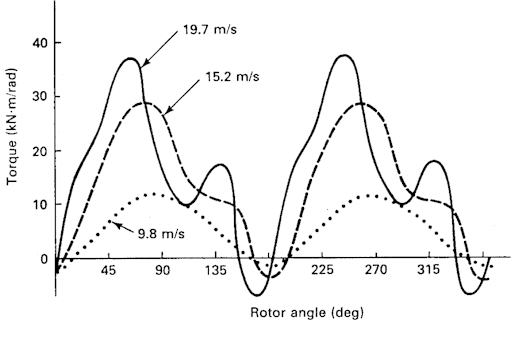
There's a pretty obvious torque ripple all right.
The unit is bound to be affected by its aspect ratio, rotational speed, solidity, and number of blades (or cylinders etc.). A change to any of these will probably have an effect on the others.
Lots of fun!
Ted.