Hi All,
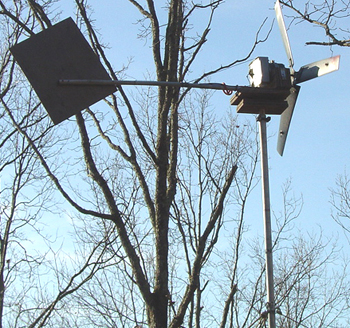
Here's one of my 2 GE ECM turbines. Yeah, it's on a short pole-tower, but it's what I got. I wish I could retro fit one with arc segment neos on the rotor. I'm sure it could get past the pitiful 5 amp limit then. I've tried Jerrys seperation of the fields and individual rectification, but I saw little or no improvement. These have a nice electronics package hung on the back, and both of mine had a single blown capacitor. I've used the mosFETs and other parts in little projects, including my Ku band sattelite reciever based solar panel tracker. I'll post my very own design for the drive schematic soon. That circuit uses the fact that the sun only travels in one direction with 2 NE555's to time control movement, (hint). I have a set of Jerrys blades on both, with my own mods. I thinned the trailing edge, rounded the tips a little, and cut off the root tab, moving the mounting bolts into the body where it's stronger, and they work sweet. I don't sandwich them, just used some good sized washers between the bolt head and blade. The hub is from a big central air conditioning fan, and fit the 1/2" motor shaft perfectly. I barely had to tweak the attack angle. You'll notice the bumps out from the root. These were balancing weights, and have been moved back in to the root since this photo. Also you'll see that one blades has a bit of red paint out towards the tip. This was a balancing aid. I could tell if the blade in front or behind the red balde was out, or the red one. I helps a lot on these blades, as the uniform blackness can make it confusing.
The pivot point is a Ford rear axle bearing sandwiched between 2 plywood plates. The lower plate has a oversized hole that doesn't touch the pole. The box on the back is a nice thick aluminum housing that hides the bridges and BIG capacitors. It also has heatsink fins in the top. That's where the origional electronics were housed. No, it does't have furling. I'm not sure I'm smart enough to build that. The tail boom is a scrap of C PVC (1") Schedule 40 with a hunk of 1/4" plywood as the tail. So far they've survived well over 80mph winds, as we had a close call with an F1 last November.
I cut 4 chunks of 3/4" plywood to match the radius of the motor and a bolt pinch strap to lock that to the motor to a doubled 3/4" plywood base where the radius parts mate to the base. All Scrap. The harware, wood, blades and everything else cost me around $45 total. So for my 12V ECM turbine I'm spending $.75 per watt, aprox.
I'm still looking for the 1 HP version of this motor, and more of this kind. But they're getting hard to find.
I'll post some more later. Thanks for the bandwidth Otherpower!
RogerAS
PS see postings:
http://www.fieldlines.com/story/2004/3/22/9835/59954
and
http://www.fieldlines.com/story/2004/3/18/113923/780